第七章
腐蝕控制
Vol.7.5
選材、腐蝕試驗及腐蝕控制
7.5.2
選材腐蝕試驗設計
材料的腐蝕試驗是檢測金屬或其他材料因與環境發生相互作用而引起的化學、電化學或物理(或機械)-化學損傷過程的材料試驗。是掌握材料與環境所構成的腐蝕體系的特性、了解腐蝕機制,從而對腐蝕過程進行控制的重要手段。
01 試驗目的
①在給定環境中的服役壽命;
②在特定環境中確定各種防蝕措施的適應性、最佳選擇、質量控制途徑和預測采取這些措施后構件的服役情況,評價材料的耐蝕性能,篩選評定各種備選材料的耐蝕性,包括腐蝕速率和局部腐蝕的可能性和速率;
③對新材料進行耐蝕性分析;
④確定環境的侵蝕性,研究環境中各組分、條件和腐蝕產物等對腐蝕速度、腐蝕形態的作用;
⑤研究腐蝕控制方法的有效性及選取最佳的控制參數;
⑥研究對腐蝕對環境或產品的污染作用;
⑦分析失效原因時作再現性試驗;
⑧檢驗材料質量的例行實驗,研究或驗證制造工藝對材料耐蝕性的影響;
⑨驗證產品的耐蝕性;
⑩研究腐蝕機理。
02 試驗方法分類
材料的耐蝕性能是與環境條件、化學、物理、機械等因素密切相關的。因此,在腐蝕試驗中必須注意試驗體系與實際工作條件盡可能有良好的一致性。為比較材料的耐蝕性能,常需要制訂標準試驗方法來概括可能的工作條件。然而,由于實際腐蝕體系的復雜性,這種方法只能近似和相對地比較所得結果。按腐蝕試驗與實際工作條件接近的程度或試驗場合的不同,試驗方法可分為實驗室試驗、現場掛片試驗和實物試驗3類。
①實驗室試驗。實驗室試驗是指在實驗室內有目的地將專門制備的小型試樣在人工配制的、受控的環境介質條件下進行的腐蝕試驗。
優點是可孤立地研究某一因素的作用或幾個因素的共同作用。為縮短試驗周期,常在不改變實際腐蝕機制的前提下強化試驗條件,進行加速腐蝕試驗。可充分利用實驗室儀器、控制設備,自由選擇試樣的大小及形狀,可嚴格地控制有關的影響因素,試驗時間較短,可精確和靈活性地進行試驗,試驗結果的重現性較好。所有,腐蝕試驗一般應先在實驗室進行,實驗室試驗有:
a.模擬試驗。是一種不加速的長期試驗,在實驗室的小型模擬裝置中,盡可能地精確地模擬自然界或工業生產中所遇到的介質及條件,雖然介質和環境條件的嚴格重現是困難的,但主要影響因素可充分考慮。這種試驗周期長,費用大,但實驗數據較可靠,重現性也高;
b.加速腐蝕試驗。是一種強化的腐蝕試驗方法,把對材料腐蝕有影響的因素如介質濃度、化學成分、溫度、流速等加以改變,使之強化腐蝕作用,從而加速整個試驗過程的進行。可在較短時間內確定材料發生某種腐蝕的傾向,或若干種材料在指定條件下的相對耐蝕順序。
缺點是只能強化一個或少數幾個控制因素。除特殊腐蝕試驗外,一般不應引入實際條件下并不存在的因素,也不能因引入了加速因素而改變實際條件下原來的腐蝕機理和特征。
②現場掛片試驗。指把專門制備的試樣置于現場的實際環境中進行的腐蝕試驗。試驗方法和過程較簡單,環境條件的真實性使它的試驗結果比較可靠,結果更具有代表性。但現場試驗中的環境因素無法控制,很難按需要來改變試驗條件,結果的重現性較差,試驗周期較長,且試驗用的試樣與實物狀態之間存在較大的差異。
在實驗室實驗獲得初步結果后,除理論研究和常規檢驗外,一般都需要進一步進行模型或現場試驗。這是因為實驗室試驗通常有加速性質,小試件的表面狀態與設備的大表面有較大的差別,試驗環境不可能模擬生產環境,在生產中的介質環境可能有變化等;
③實物試驗。指將試驗材料制成實物部件、設備或小型試驗性裝置,在現場的實際應用下進行的腐蝕試驗。解決了實驗室試驗及現場試驗中難以全面模擬的問題,而且包括了結構件在加工過程中所受的影響,能夠較全面正確地反映材料在使用條件下的耐蝕性。但費用較大,試驗周期長,且不能對幾種材料同時進行對比試驗。因此,實物試驗應在實驗室試驗和現場試驗的基礎上進行。
自然環境中的暴露試驗周期都很長,如在大氣或海洋中觀察試件的失重和外觀變化,試驗周期可長達20~30a以上。實驗數據的積累是一項重要的工作。
03 試樣的準備
①試樣材料。對所用試樣的各種原始資料應盡可能地詳細了解,其中包括材料的牌號、化學成分和力學性能等,對于金屬還應包括試樣的冶金和加工工藝特征、熱處理及金相組織等。這些資料的了解,對于腐蝕結果的分析有重要的參考作用;
②試樣的形狀與尺寸。取決于試驗的目的、試驗的方法、材料的性質、試驗的時間和試驗的裝置等。試樣的外形要求簡單,以便于精確測量表面積、清除腐蝕產物和進行加工。
為消除邊界效應的影響,試樣表面積對邊緣面積之比應盡量大,試樣表面積對試樣重量之比也要盡量大些。
通常實驗室所用的試樣尺寸為:矩形 50mm×25mm×(2-3)mm,圓盤形Φ(30-40)mm×(2-3)mm,圓柱形Φ10mm×20mm,等;
③試樣的表面處理。試樣表面的粗糙度、均一性和潔凈程度是影響腐蝕實驗結果重現性和可比性的重要因素,因此在試驗前應經過嚴格的表面處理。
通常從原材料上切取試板、經適當的機械加工和必要的研磨拋光制成試樣,再經統一的清洗使之具有相近的表面狀態;
④平行試樣的數量。為提高試驗結果的準確性,每次試驗時須用一定數量的平行試樣。平行試樣越多,結果的準確性就越高。
通常一般試驗的平行試樣為3-12個,常用5個,最少3個。加載應力試驗,試樣為5-20個,常用10個,最少3個。在同一試驗容器中只可進行1個或幾個同一材質的平行試樣的腐蝕試驗。
04 腐蝕的暴露條件
①腐蝕介質
a. 直接取自生產現場;
b. 按現場介質成分人工配制,應當用蒸餾水和純度為化學純以上試劑精確地配制試驗溶液,以嚴格控制試液的成分。
在試驗過程中,還必須防止由于溶液蒸發及其它原因引起介質濃度、成分和體積的變化,以免影響介質的腐蝕性能和結果的可靠性。介質體積與試樣面積比須符合標準的規定。
②試驗溫度。
腐蝕試驗溫度應盡量模擬實際腐蝕介質的溫度。實驗室控溫方法有水浴、油浴或空氣恒溫箱等。控制的溫度應是整個試樣的表面溫度,但為簡便起見,往往以介質溫度為控制對象。
③試驗時間。
材料的全面腐蝕速率很少是恒定不變的,經常隨時間而不斷變化,因此試驗的時間一般取決于材料的腐蝕速度。
局部腐蝕試驗時間應按相關試驗標準進行。全面腐蝕試驗在實驗室里一個周期的試驗時間通常為24-168h,即1-7d。如果腐蝕速度是中等以下,則可由下式粗略地估計試驗時間,該式僅適用于已知大概腐蝕速率的試驗。
試驗時間(h)=50/腐蝕速率(mm·a-1) (7-1)
④試樣暴露的條件。
在實驗室試驗中,根據試驗目的的不同,試樣可全部(全浸)、部分(半浸)或間斷(間浸)暴露于腐蝕介質中,以模擬實際應用中可能遇到的各種情況。
⑤試樣安放與涂封。
a. 防止電偶效應。試樣的安放應保證試樣與試樣之間、試樣與容器之間、試樣與支架之間電絕緣;保證試樣有恒定的暴露面積,用絕緣材料將試樣部分表面涂封遮蔽。在進行電化學測試時,必須在試樣上引出導線,導線和試樣的結點必須涂封,以防電偶腐蝕的干擾。涂封要求絕緣好、牢固、簡便;
b. 防止縫隙腐蝕。試樣與試樣之間、試樣與容器之間、試樣與支架之間不產生縫隙,試樣表面與介質充分接觸。同時,要求試樣裝取方便、牢固可靠;支架本身耐蝕等;
c. 防止水線腐蝕(濃差腐蝕)。
05 腐蝕結果評定
①全面腐蝕速率。常用的腐蝕速率評定方法有失重法、線性極化法、電阻法和塔費爾極化曲線外推法等;
②孔蝕的評定。孔蝕試驗的試樣比失重試樣大,一般約數十平方厘米。評定指標有:最大孔蝕深度、平均孔蝕深度、孔蝕密度和單位面積失重等;
③晶間腐蝕試驗。一般腐蝕試驗都可以用來檢查晶間腐蝕。可用拉伸或彎曲試驗評定晶間腐蝕引起的力學性能損失,或用金相顯微鏡觀察晶間的腐蝕情況;
④應力腐蝕試驗。應力腐蝕試驗方法有很多種,試樣也有多種類型,適用于各自特定目的,其加載應力、腐蝕暴露方法和時間、計算應力和評定結果的方式各不相同,其特點和局限性也不同,須根據試驗目的和實際條件來選擇加載方式、試樣類型和試驗方法。一般,按載荷加載方式來分有恒載荷、恒變形、慢應變速率3種。而具體試樣的類型又可以分成以下幾種:光滑試樣,彎梁試樣、C形環試樣、U形試樣和O形試樣;缺口試樣;預裂紋試樣,增K型試樣、恒K型試樣、降K形試樣。
a. 慢拉伸速率試驗(SSRT)。是將拉伸試樣放在特定介質中,通過慢拉伸速率拉伸試驗機,以一個相當緩慢的應變速率對置于應力腐蝕環境中的試樣施加應力,通過強化應變狀態來加速腐蝕裂紋的發生和發展過程。SSRT方法提供了在傳統應力腐蝕試驗不能迅速激發應力腐蝕的環境里確定延性材料應力腐蝕敏感性的快速試驗方法,它能使任何試樣在較短時間內發生斷裂,因此是一種相當苛刻的加速試驗方法。SSRT的提出者認為:在發生應力腐蝕體系中,應力的作用是為了促進應變速度,真正控制應力腐蝕裂紋產生和擴展的參數是應變速率而不是應力本身。
不同的行業,不同的材料有不同的慢應變速率應力腐蝕試驗標準,試驗標準有ISO 7539.7[1]、GB/T 15970.7[2]、HB 7235[3]、HB 5260[4]等。慢應變速率法中應變速率的確定至關重要,如果應變速率過快,則試樣來不及產生有效的應力腐蝕,就已經產生韌性斷裂;如果應變速率過慢,在試樣表面膜破裂后來不及產生有效的腐蝕,裸露的金屬就再發生鈍化,使應力腐蝕不發生,最后也將產生韌性斷裂。不同的腐蝕體系采用的臨界應變速率也不一樣,表7-10。
表7-10 不同腐蝕體系SSRT臨界應變速率
慢應變速率法應力腐蝕敏感性表征參量,通常以慢應變速率試驗結果與在不發生應力腐蝕的惰性介質(如油或空氣)中的試驗結果進行比較,以兩者在相同溫度和應變速率下的試驗結果的相對值表征應力腐蝕的敏感性。主要有以下幾個評定指標:
i.斷裂應力:在腐蝕介質中和惰性介質中的斷裂應力比值愈小,應力腐蝕敏感性就愈大;
ii.斷裂時間:從開始試驗到載荷達到最大值時所需的時間t。應變速率相同時,腐蝕介質中和惰性介質中斷裂時間比值愈小,則應力腐蝕敏感性愈大;
iii.吸收的能量:應力-應變曲線下的面積代表試樣斷裂前吸收的能量。惰性介質(空氣)和腐蝕介質試驗中吸收能量差別愈大,應力腐蝕敏感性也愈大;
iv.塑性損失:用腐蝕介質和惰性介質中的延伸率、斷面收縮率的相對差值來度量應力腐蝕敏感性;
v.斷口形貌:對大多數壓力容器鋼材,在惰性介質中斷裂后將獲得韌窩性斷口,而在腐蝕介質中,拉斷后往往獲得脆性斷口。其中脆性比例愈高,則應力腐蝕愈敏感。如介質中拉斷后斷面存在二次裂紋,也可以用二次裂紋的長度和數量來衡量應力腐蝕的敏感性。
在載荷-拉伸曲線上,將在惰性介質中的各特征參數與在腐蝕介質中的特征參數進行SSRT試驗結果評定:
ISCC =(I惰-I腐)/ I惰 ×100% (7-2)
式中 ISCC-應力腐蝕敏感性指數;
I惰-在惰性介質中的試驗參數;
I腐-在腐蝕介質中的試驗參數。
評定應力腐蝕開裂敏感性指數ISCC,目前比較認可的參數有:ReL、Rm、A、Z、da/dt、內積功。ISCC衡量應力腐蝕開裂敏感性大小的一般評定:
當ISCC 大于35%,研究體系具有明顯的應力腐蝕傾向;
當ISCC介于25%~35% 之間,研究體系有應力腐蝕傾向;
當ISCC 小于25%,研究體系沒有明顯的應力腐蝕傾向
b. 斷裂力學方法。運用斷裂力學理論,研究應力腐蝕開裂,不僅可以定量地測定材料在特定環境中的應力腐蝕開裂門檻應力強度因子KISCC,而且能夠測定材料在特定環境介質中的裂紋擴展速率da/dt。KISCC標志著結構件中可以存在而又不引起應力腐蝕裂紋擴展的最大缺陷的尺寸,也就是規定了允許的最大臨界尺寸,da/dt反映了材料在環境介質中抗開裂的能力,這兩個重要參數可直接提供工程設計和材料研究使用,具有相當大的實際意義。
材料在應力腐蝕破壞過程中,其破壞壽命包括裂紋擴展前的孕育期和裂紋慢擴展期兩部分組成。如果已經測得了裂紋擴展速率da/dt,那么就可以估算構件材料的安全使用期。為了測定應力腐蝕裂紋擴展速率,Brown等人于1965年首先使用WOL型試樣采用了恒定位移法進行了研究。恒位移試樣具有以下優點:
i.用螺釘自行加載,故不需要用試驗機,可以大批量測試。特別是可以把試樣放在實際使用的環境中做試驗,從而可以獲得現場條件下的試驗數據;
ii.隨著裂紋擴展,恒位移試樣的KI下降,當降到KISCC時裂紋將停止擴展。因此用1個試樣就可以測出止裂的KISCC,同時也可測出da/dt;
iii.可帶載荷在顯微鏡下直接觀察裂紋的形核和擴展過程;
iv.對于WOL試樣,也可在線切割后不預制裂紋,但不能加載到出現裂紋,只要初始KI略大些或經過長的孕育期后就可從缺口處產生滯后裂紋。一旦出現裂紋后再降低Vo(即降低初始值),則裂紋在擴展一段長度后就會止裂,由此可得KISCC。
c.各種SCC試驗方法對比。以加載方式區分的3種SCC物理試驗方法的評定方式、優缺點特征列于表7-11中。因為各種試驗方法的評定對象和優缺點各不相同,所以實際選用時要考慮到材料、介質、試驗要求等多方而的因素,選用合適的試驗方法。
表7-11 應力腐蝕試驗方法的特點
06 腐蝕試驗設計
試驗設計在科學實驗、工業生產和工程設計中能發揮重要的作用,例如:提高產量;減少質量的波動,提高產品質量;大大縮短新產品試驗周期;降低成本;延長產品壽命等。
試驗設計方法是一套完整的系統方法,如何安排實驗,使實驗次數盡量少,而又能達到好的試驗效果,這是經常會碰到的問題。解決這個問題有一門專門的學問即“試驗設計”。上世紀30年代,由于農業試驗的需要,費歇(R.A.Fisher)在試驗設計和統計分析方面做出了一系列先驅工作,從此,試驗設計成為統計科學的一個分支。
60年代,華羅庚教授在我國倡導與普及的“優選法”,與我國的數理統計學者在工業部門中普及的“正交設計”法都是試驗設計方法。這些方法經普及后,已為廣大技術人員與科學工作者掌握,取得一系列成就,產生了巨大的社會效益和經濟效益。“優選法”是單變量的最優調試法,即假定我們處理的實際問題中只有一個因素起作用,但這種情況幾乎是沒有的,所以在使用時,只能抓“主要矛盾”,即突出一個因素,而將其他因素固定,這樣來安排實驗。因此“優選法”還不是一個很精確的近似方法。
“正交設計”的基礎是拉丁方理論與群論,可以用來安排多因素的試驗,而且試驗次數對各因素的各水平的所有組合數來說是大大地減少了,但對于某些工業試驗與昂貴的科學實驗來說,試驗仍嫌太多,而無法安排。
1978年,七機部由于導彈設計的要求,提出了一個5因素的試驗,希望每個因素的水平數要多于10,而試驗總數又不超過50,顯然優選法和正交設計都不能用,王元和方開泰提出了一個新的試驗設計,即所謂“均勻設計”,將這一方法用于導彈設計,取得了成效。均勻設計屬于近40年發展起來的“偽蒙特卡羅方法”的范籌,將經典的確定的單變量問題的計算方法推廣后用于多變量問題的計算時,計算量往往跟變量個數有關。烏拉母(S.Ulam)與馮諾依曼(J.von Neumann)在40年代提出蒙特卡羅方法,即統計模擬方法,這個方法的大意是將一個分析問題化為一個有同樣解答的概率問題,然后用統計模擬的方法來處理后面這個問題,這樣使一些困難的分析問題反而得到了解決,例如多重定積分的近似計算。蒙特卡羅方法的關鍵是找一組隨機數作為統計模擬之用,所以這一方法的精度在于隨機數的均勻性與獨立性。不論是均勻設計或配方均勻設計,其數據分析都要藉助于回歸分析,要用到線性回歸模型、二次回歸模型、非線性模型,以及各種選擇回歸變量的方法(如前進法、后退法、逐步回歸、最優回歸子集等)。
影響腐蝕的因素眾多,要通過試驗來摸索,試驗設計得好,則會事半功倍。均勻設計的思想也能用于配方試驗,已在我國包括腐蝕研究的領域有較廣泛的普及與使用[5],取得了一系列可喜的成績。
但均勻設計只具有充分均勻性,而正交設計還具有齊整可比性。試驗設計傾向對不同的方法取長補短,在不同階段適當結合。均勻設計的分批是按試驗結果直接逼近最優點,經計算機驗證可知,均勻設計的分散性程度很強,突出性效果亦很好,因此特別在試驗前期可以出一些好結果。但是對出好成果的均勻設計若改用正交設計,其平均效果可能也會很好。用均勻設計和正交設計從事開發工作,遠比不采用設計好得多[6]。
①試驗的因素和水平
a. 因素:在實驗中,影響試驗考核指該指標的量稱為因素,因素是自變量(Xs),如試驗中的材料、時間、溫度、成分、濃度、流速、pH值等。通常將固定的因素在試驗方案中并不稱為因素,只有變化的因素才稱為因素,固定因素稱為因子;
b. 水平:是試驗中各因素的不同取值,這些值稱做該因素的水平。如因素A、B、C均有3個取值,D、E均有6個取值等。為了便于試驗的安排,每個因素要根據以往的經驗來選擇一個試驗范圍,然后在試驗范圍內挑出幾個有代表性的值來進行試驗。
②因素和水平的選擇
選擇因素和水平是關系到一個試驗能否成功的關鍵,使用試驗設計應注意:
a. 因素選擇。在一項試驗中,應由有經驗的研究人員和工人共同討論決定從眾多的有關因子中挑選出試驗方案中的因素,在一次試驗中,因素不宜選得太多(如超過10個),否則可能會造成主次不分。相反地,因素也不宜選得太少,如只選定1、2個因素,這樣可能會遺漏重要的因素,或遺漏因素間的交互作用,使試驗的結果達不到預期的目的。因素和水平的含意可以是廣義的。例如5種材料用于試驗,要比較不同材料的耐蝕性,這時“材料品種”可設定為1個因素,5種材料就是該因素下的5個水平 。
在試驗設計時,試驗因素(輸入變量)有兩種,一種是在試驗時可以人為進行控制的,稱可控因素;一種是人為無法控制的,稱噪聲(隨機)因素;
b. 試驗的范圍控制。如果試驗在試驗室進行,試驗范圍大比較容易實現;如果試驗直接在生產中進行,則試驗范圍不宜太大,以防產生過多次品,或產生危險。試驗范圍太小,不易獲得比已有條件有顯著改善的結果。歷史上有些重大的發明和發現,是由于“事故”而獲得的,也就是說試驗的范圍大大不同于有經驗的范圍;
c. 試驗范圍和每一因素的水平個數應匹配。試驗設計的目的在于捕捉各試驗因素對輸出變量的最大影響,因此在選擇試驗因素的水平時,水平范圍要足夠寬,否則就可出現縮小甚至抵削變量影響,同時也看不出因素間交互作用對輸出的影響。當然因素水平設置也不可過寬,否則同樣可能縮小此因素的影響,或將其它因素的影響掩蓋掉。過寬還可能超出允許操作范圍,造成意外損失;
d. 水平的間隔和生產控制精度是密切相關的。如壓力容器的工藝物料溫度設定控制在100℃,控制精度只能作到±5℃,于是在生產過程中溫度將會在100℃±5℃,即95-105℃波動。則試驗溫度設定的3個水平95℃、100℃、105℃之間間隔太小,應當加大,如90℃、100℃、110℃。
③因素的主效應和因素間的交互效應
在試驗中用來衡量試驗結果的量叫試驗指標,在數理統計中,稱試驗指標為響應(response)。根據試驗的目的,要預先確定一項或多項試驗指標。
由于試驗中總存在一些偶然因素的干擾,如室溫變化、介質濃度波動、材料的不均勻性,這些偶然因素總稱為隨機誤差。由于試驗誤差的存在,不可能產生理想的情況。實際上,當試驗的水平和相應的結果為連續變量時,其數學模型也可以用回歸方程來表達。有一點必須注意的是,模型中的主效應或模型中的線性回歸效應都強烈地依賴于試驗條件、試驗范圍。實際情況是多種多樣的,例如X和Y之間可能有非線性回歸關系,或其它相關關系。
④因素間交互作用的概念
首先,設有兩個因素A和B它們各取2個水平A1、A2和B1、B2。這時共有4種不同的水平組合,其試驗結果如圖7-13。當B=B1時,A1變到A2使Y增加30-10=20;類似地,當B=B2時,A1變到A2使Y也增加40-20=20。這就是說A對Y的影響與B取什么水平無關,圖7-13a。類似地,當B從B1變到B2時,Y增加20-10(或40-30=10),與A取的水平無關。這時,我們稱A和B之間無交互作用。判斷A和B之間有沒有交互作用,選用圖7-13b的作圖方法更為直觀。當圖中的兩條線平行時(或接近平行時),判斷A和B之間沒有交互作用,圖7-13c、d給出了一個有交互作用的例子。
a. A和B之間無交互作用 b. A和B之間無交互作用
c. A和B之間有交互作用 d. A和B之間有交互作用
圖7-13 因素間交互作用
交互作用在實際中是大量存在的,特別是在腐蝕試驗中,許多因素間都有交互作用。當因素A、B 及其它們的試驗指標Y都為連續變量時,可以建立Y和A、B之間的回歸方程。若回歸方程為式(7-3)時A對Y的影響由回歸系數β完全決定,不受B取哪個水平的影響;同樣,B對Y的影響由回歸系數γ完全決定,不受A取哪個水平的影響;類似地,對Y的影響由回歸系數α決定,不受取哪個水平的影響。這時A和B沒有交互作用。
當A和B之間有交互作用時,回歸模型不可能為線性的,其中一定有非線性的。最常見的模型之一為:
式中α、β、γ、δ為回歸系數,ε為隨機誤差。這時若δ>0,稱A和B之間有正交互作用;若δ<0,稱A和B之間有負交互作用。
⑤全面試驗和多次單因素試驗
在一項試驗中,當因素和水平確定后,如何設計該項試驗主要有兩種方法:
a. 全面試驗。該方法將每一個因素的不同水平組合做同樣數目的試驗,例如將每個因素的不同水平組合均作一次試驗。在一項試驗中若有m個因素, 它們各有l1…lm個水平, 則全面試驗至少需做l1×l2…×lm次試驗。當因素的個數不多,每個因數的水平數也不多時,常用全面試驗的方法,并且通過數據分析可以獲得較為豐富的結果,結論也比較精確。當因數較多,水平數較大時,全面試驗要求較多的試驗。對絕大多數場合,做這么多次試驗是不可能的。
b. 多次單因素試驗。這個方法在工程和科學試驗中常被人們所采用。當因素之間沒交互作用時,這個結論是正確的;當因素之間有交互作用時,該結論一般不真。因此,多次單因素試驗法有局限性。特別是,當因素的數目和水平數更多時,常常會得到錯誤的結論,不能達到預期的目的。
c. 正交試驗法(正交設計)。所有的試驗設計方法本質上就是在試驗的范圍內給出挑選代表點的方法。正交設計是根據正交性準則來挑選代表點,使得這些點能反映試驗范圍內各因素和試驗指標的關系。統計學家將正交設計通過一系列表格來實現,這些表叫做正交表。例如表7-12就是一個正交表,并記為L9(34),這里“L”表示正交表“9”表示總共要作9次試驗,“3”表示每個因素都有3個水平,“4”表示這個表有4列,最多可以安排4個因素。還有一批混合水平的表在實際中也十分有用,如 L8(4×24)、L12(23×3)、L16(44×23)等。
表7-12 正交表 L9(34)
在表7-13的正交試驗設計中,可以看到有如下的特點:每個因素的水平都重復了3次試驗、每兩個因素的水平組成一個全面試驗方案。這2個特點使試驗點在試驗范圍內排列規律整齊,稱為“整齊可比”。另一方面,如果將正交設計的9個試驗點點成圖(圖7-14),我們發現9個試驗點在試驗范圍內散布均勻,這個特點被稱為“均勻分散”。正交設計的優點本質上來自“均勻分散,整齊可比”這兩個特點。
圖7-14 正交設計均勻分散性
d. 均勻設計。正交設計在挑選代表點時有兩個特點:均勻分散,整齊可比。“均勻分散”使試驗點有代表性;“整齊可比”便于試驗數據的分析。為了保證“整齊可比”的特點,若在一項試驗中有s 個因素,每個因素各有q 水平,用正交試驗安排試驗,則至少要作q2個試驗,當q 較大時,q2將更大。對這一類試驗,若要減少試驗的數目,只有去掉整齊可比的要求。
均勻設計就是只考慮試驗點在試驗范圍內均勻散布的一種試驗設計方法,和正交設計相似,也是通過一套表來進行試驗設計的,每一個均勻設計表有一個代號Un(qs)或U*n(qs),其中“U”表示均勻設計,“n” 表示要做n 次試驗,“q”表示每個因素有q個水平,“s”表示該表有s列。的右上角加“*”和不加“*”代表兩種不同類型的均勻設計表,如表7-13。通常加“*”的均勻設計表有更好的均勻性,應優先選用。
每個均勻設計表都附有一個使用表,它指示我們如何從設計表中選用適當的列,以及由這些列所組成的試驗方案的均勻度。如表U*6(64)最多可以安排4個因素的試驗。若用正交表安排3個6水平因素,至少要采用L36(63),該表最多能安排3個因素,可要做36次試驗,而兩個表的偏差一個為0.1875(U*6),另一個為0.1597(L36),相差并不十分大。由此例可見均勻設計的優點。表7-14是U*6(64)的使用表,它告訴我們,若有2個因素,應選用1,3兩列來安排試驗;若有3個因素,應選用1,2,3三列,…,最后1列D表示刻劃均勻度的偏差(discrepancy),偏差值越小,表示均勻度越好。當試驗數n給定時,通常Un表比U*n表能安排更多的因素。故當因素s較大,且超過U*n的使用范圍時可使用Un表。
表7-13 U*7(74)
表7-14 U*6(64)的使用表
均勻設計有其獨特的布(試驗)點方式,其特點表現在:每個因素的每個水平做一次且僅做一次試驗。任2個因素的試驗點點在平面的格子點上,每行每列有且僅有一個試驗點,如表U*6(66)的第一列和第三列點成圖7-15a;這兩個特點反映了試驗安排的“均衡性”,即對各因素,每個因素的每個水平一視同仁;均勻設計表任兩列組成的試驗方案一般并不等價,例如用U*6(66)的1,3 和1,4列分別畫圖,得圖7-15a、b。可見a的點散布比較均勻,而b的點散布并不均勻。均勻設計表的這一性質和正交表有很大的不同,因此,每個均勻設計表必須有一個附加的使用表。
圖7-15 均勻設計的均衡性
當因素的水平數增加時,試驗數按水平數的增加量在增加。如當水平數從9水平增加到10水平時,試驗數n 也從9增加到10。而正交設計當水平增加時,試驗數按水平數的平方的比例在增加。當水平數從9到10時,試驗數將從81增加到100。由于這個特點,使均勻設計更便于使用。
均勻設計表的使用步驟和正交設計很相似,但也有一些不同之處。通常有如下步驟:
i.根據試驗的目的,選擇合適的因素和相應的水平;
ii.選擇適合該試驗的均勻設計表,然后根據該表的使用表從中選出列號,將因素分別安排到這些列號上,并將這些因素的水平按所在列的指示分別對號。
參考文獻
[1] ISO 7539.7-2005.Corrosion of metals and alloys – Stress corrosion testing Part7: Method for slow strain rate testing
[2] GB/T 15970.7 -2017.金屬和合金的腐蝕 應力腐蝕試驗 第7部分:慢應變速率試驗
[3] HB 7235-1995.慢應變速率應力腐蝕試驗方法10
[4] HB 5260-1983.馬氏體不銹鋼拉伸應力腐蝕試驗方法
[5] 盧志明,朱建新,高增梁。 16MnR鋼在濕硫化氫環境中的應力腐蝕開裂敏感性研究[J].腐蝕科學與防護技術,2007,19(6):410-413
[6]夏之寧,堪其亭,穆小靜,等。正交設計與均勻設計的初步比較[J].重慶人學學報(自然科學版),1999,22(5):112-117
免責聲明:本網站所轉載的文字、圖片與視頻資料版權歸原創作者所有,如果涉及侵權,請第一時間聯系本網刪除。
相關文章
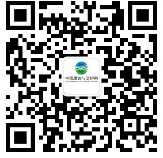
官方微信
《中國腐蝕與防護網電子期刊》征訂啟事
- 投稿聯系:編輯部
- 電話:010-62316606-806
- 郵箱:fsfhzy666@163.com
- 中國腐蝕與防護網官方QQ群:140808414
點擊排行
PPT新聞
“海洋金屬”——鈦合金在艦船的
點擊數:7343
腐蝕與“海上絲綢之路”
點擊數:5905