摘要
采用傳統的硫酸陽極氧化工藝對2E12航空鋁合金進行處理,在鋁合金表面制備了一層陽極氧化膜。研究了表面包鋁層和陽極氧化時間對鋁合金氧化膜表面形貌和硬度的影響,并探討了硫酸陽極氧化處理對鋁合金拉伸性能和疲勞性能的影響規律及機制。結果表明,2E12鋁合金基體中的第二相在陽極氧化過程中會發生溶解,使得氧化膜表面出現孔洞。隨著氧化時間的延長,氧化膜的厚度逐漸增加,孔洞數量也增多且尺寸變大。2E12鋁合金經硫酸陽極氧化處理后,拉伸性能基本保持不變,但疲勞壽命出現明顯下降。其中,去除包鋁層的2E12鋁合金經陽極氧化后,疲勞壽命最高下降到陽極氧化前的30%。硫酸陽極氧化處理后,疲勞裂紋起源于氧化膜表面的缺陷處,疲勞斷口呈現多個裂紋源的特征。
關鍵詞: 航空鋁合金 ; 硫酸陽極氧化 ; 疲勞壽命 ; 包鋁層
2xxx系鋁合金具有較高的比強度以及優異的綜合性能,廣泛應用于航空航天領域,如2A12鋁合金薄板廣泛應用于飛機蒙皮。2E12鋁合金是在2A12合金的基礎上,降低Fe和Si等有害雜質元素的含量,調整優化Cu和Mg等主合金元素的含量而開發出的一種新型高純鋁合金。2E12鋁合金在保證強度水平與2A12鋁合金相當的基礎上,疲勞性能和斷裂韌性得到明顯改善,尤其抗疲勞裂紋擴展性能優良,是一種新型具有高損傷容限合金,被認為是新一代飛機蒙皮的優選材料[1,2,3]。
2系鋁合金為鋁銅合金,耐腐蝕性能稍弱。為了提高其耐腐蝕性能并延長服役壽命,通常會在薄板表面包覆一層純鋁,可以為基體材料提供腐蝕防護作用。此外,包鋁層含有較少的金屬間化合物,也會進一步防止材料發生局部腐蝕[4,5]。同時,在零件制造過程中要進行硫酸陽極氧化處理,可在鋁合金表面形成一層陽極氧化膜,進一步提高鋁合金的耐腐蝕性能。2E12鋁合金中Cu含量較高,主要強化的合金相也是含Cu相。但在陽極氧化過程中,Cu會在基體和氧化膜界面富集,然后Cu發生氧化,氣體逸出,使得形成的氧化膜中存在缺陷,導致氧化膜硬度、耐腐蝕性能以及合金力學性能下降[6,7,8]。張艷斌等[9]對2014-T6鋁合金進行硫酸陽極氧化處理,在合金表面制得5,10和15 μm的氧化膜。結果表明,當合金表面氧化膜較厚時,氧化膜中會出現龜裂狀裂紋。在中低應力作用下,陽極氧化處理會大幅降低鋁合金的彎曲疲勞性能;而在高應力作用下,陽極氧化對鋁合金彎曲疲勞性能的影響不明顯。當鋁合金表面氧化膜較薄時,疲勞裂紋起源于氧化膜表面;而當氧化膜較厚時,疲勞裂紋起源于鋁合金基體表面。作者所在課題組曾對比研究了硫酸-己二酸陽極氧化、硫酸陽極氧化和鉻酸陽極氧化對LY12CZ鋁合金軋制板材疲勞性能的影響[10]。結果表明,陽極氧化會造成鋁合金疲勞壽命下降,其中傳統硫酸陽極氧化工藝影響程度最大,而鉻酸陽極氧化的影響程度最小;在硫酸電解液中添加己二酸后,生成的氧化膜中孔洞和缺陷尺寸減小,一定程度上抑制了疲勞裂紋的萌生,從而提高了疲勞壽命。
本文研究了表面包鋁層、陽極氧化時間對2E12鋁合金硫酸陽極氧化膜表面形貌及厚度的影響,并探討了硫酸陽極氧化處理對鋁合金拉伸性能和疲勞性能的影響規律及機制。
1 實驗方法
1.1 實驗材料
本實驗所選用的材料為表面帶包鋁的2E12-T3鋁合金軋制薄板,厚度為2.5 mm,表面包鋁層厚度大約為70 μm。鋁合金名義成分 (質量分數,%) 為:Cu 4.0~4.5,Mn 0.45~0.7,Mg 1.2~1.6,Cr≤0.05,Zn≤0.15,Ti≤0.10,Fe≤0.12,Si≤0.06,Al 余量。將部分表面帶包鋁的2E12鋁合金試樣,放入50 °C的50 g/L NaOH溶液中浸泡20~30 min,清水沖洗后,再在400 g/L的HNO3溶液中出光至表面光亮,然后采用SiC砂紙將試樣連續打磨到1200#,作為去除包鋁層的2E12鋁合金試樣。去除包鋁層后的試樣厚度介于2.2~2.3 mm之間,表面包鋁層已完全去除。最后將表面帶包鋁及去除包鋁后的試樣分別在無水乙醇和去離子水中超聲清洗10 min,并吹干備用。
1.2 陽極氧化
硫酸陽極氧化工藝為:除油→堿洗→硝酸出光→硫酸陽極氧化→沸水封閉。每一步工藝結束后都在流動熱水以及流動冷水中清洗試樣,再進行下一步操作。其中除油、堿洗、出光等陽極氧化前處理工藝中的溶液組成以及處理時間見表1。陽極氧化液為180 g/L的硫酸溶液,采用恒壓陽極氧化工藝,電壓為15 V,氧化時間分別為15,30,45和60 min,電壓緩升時間為5 min,溫度為室溫。同時在陽極氧化過程中,采用磁力攪拌器進行攪拌,加快散熱,保證氧化溫度穩定。保留包鋁層以及去除包鋁層的2E12鋁合金試樣經上述陽極氧化工藝處理后,再用去離子水清洗干凈,在95~100 °C的微沸去離子水中封閉處理30 min。采用渦流測厚儀測試氧化膜層的厚度。
表1 前處理溶液的化學組成,處理時間和溫度
1.3 形貌觀察
陽極氧化后的2E12鋁合金試樣經噴金處理后,使用JEOLJSM-7500型場發射掃描電子顯微鏡 (FE-SEM) 對陽極氧化膜層的表面和截面形貌進行觀察分析。
1.4 拉伸及疲勞性能測試
拉伸和疲勞實驗取樣方向均為沿板材的橫向。參考GB/T 228[11],采用INSTRON 5887電子萬能材料試驗機進行拉伸性能測試,拉伸實驗的試樣尺寸見圖1。參考HB 5287[12],采用MTS 810疲勞試驗機進行疲勞性能測試,采用恒幅載荷,應力比R=0.1,最大應力σmax=300 MPa,實驗頻率為110 Hz,試樣尺寸見圖2。疲勞實驗中,同一個應力下進行5組測試,且需滿足95%的置信度,通過試樣的中值疲勞壽命評價陽極氧化對鋁合金疲勞性能的影響。
圖1 拉伸試樣示意圖
圖2 疲勞試樣示意圖
2 結果與討論
2.1 包鋁層和陽極氧化時間對2E12鋁合金氧化膜厚度的影響
帶包鋁層和去除包鋁層的2E12鋁合金經硫酸陽極氧化處理15,30,45和60 min后膜層厚度與氧化時間的對應關系見圖3。可以看出,帶包鋁層和去除包鋁層的2E12鋁合金表面氧化膜的厚度均隨著氧化時間的延長而增加,其中帶包鋁層的氧化膜厚度由13.24 μm (15 min) 逐漸增加到35.32 μm (60 min);去除包鋁層的氧化膜厚度由7.76 μm (15 min) 逐漸增加到15.01 μm (60 min)。相同陽極氧化時間條件下,帶包鋁層合金的表面氧化膜明顯厚于去除包鋁層合金的。對于去除包鋁層的2E12鋁合金,當陽極氧化時間達到45 min后,氧化膜厚度增加的趨勢明顯變緩。
圖3 氧化膜厚度與氧化時間的關系
2E12鋁合金表面包鋁層為一層純Al,而去除表面包鋁層后,露出了合金基體。由于合金基體中含Cu合金相的氧化Gibbs自由能高于Al的,故成膜效率較低,因而膜層也較薄。在陽極氧化過程中,同時存在著氧化膜的生長與溶解過程,當氧化膜的生長速率大于溶解速率時,氧化膜的厚度不斷增加;但當氧化時間繼續延長,氧化膜溶解速率加快,表面氧化膜厚度增加趨緩,最終趨于穩定。
2.2 包鋁層和陽極氧化時間對2E12鋁合金氧化膜形貌的影響
圖4為去除包鋁層和帶包鋁層的2E12鋁合金分別經陽極氧化處理15,30,45和60 min后的表面SEM形貌圖。可以看到,去除包鋁層的2E12鋁合金經硫酸陽極氧化不同時間后,表面均出現大量隨機分布、尺寸大小不一的孔洞。當氧化時間為45和60 min時,氧化膜表面甚至出現微裂紋。而對于帶包鋁層的2E12鋁合金經不同時間陽極氧化處理后,氧化膜形貌均勻,孔洞數量以及尺寸均比去除包鋁層合金的要少,也未見氧化膜開裂;但隨著氧化時間的延長,孔洞的數量增加、尺寸變大。可見,隨著氧化時間的延長,去除包鋁層和帶包鋁層的合金表面氧化膜的孔洞尺寸均變大,數量增加,但帶包鋁層的合金表面氧化膜中的孔洞更少。
圖4 去除包鋁層和保留包鋁層的2E12鋁合金經不同時間陽極氧化后的表面SEM像
對于去除包鋁層的2E12鋁合金,在陽極氧化過程中,鋁合金基體中的S(Al2CuMg) 相,作為陽極,會發生優先溶解,形成孔洞缺陷;θ(Al2Cu) 相作為陰極,由于具有較高的惰性,發生氧化反應所需要的Gibbs自由能會高于鋁發生氧化所需要的Gibbs自由能,不易發生氧化。故而,隨著鋁合金氧化的進行,會產生Cu的富集。當Cu原子的富集達到一定程度時,會發生氧化,并且進入氧化膜中。同時伴隨著O2的產生,且隨著氧化的進行O2變得更富集,則內部的氣壓會升高,最終會導致氧化膜的破裂和O2的釋放[13,14,15]。而對于帶包鋁層的2E12鋁合金,由于表面包覆著一層厚約70 μm、純度99%的純Al層,其中合金相和雜質元素含量較低,因而膜層中的孔洞數量少、尺寸小。
2.3 包鋁層和陽極氧化時間對2E12鋁合金拉伸性能的影響
陽極氧化前后的去除包鋁層和帶包鋁層的2E12鋁合金的拉伸性能測試結果見表2。可以看到,對于去除包鋁層的2E12鋁合金,經硫酸陽極氧化處理后,抗拉強度、斷后伸長率、屈服強度均有一定程度下降,但下降幅度不大。抗拉強度由最高471 MPa下降到461 MPa (陽極氧化處理45 min),下降幅度僅為2%。屈服強度由329 MPa最高下降到321 MPa (陽極氧化處理45 min),下降幅度也僅為2%。斷后伸長率由最高21.3%下降到19.4% (陽極氧化處理45 min),下降幅度達9%。而對于帶包鋁層的2E12鋁合金,經硫酸陽極氧化處理后,抗拉強度、屈服強度基本保持穩定,未呈現下降或上升趨勢。但斷后伸長率由最高21.4%下降到18.1% (陽極氧化處理45 min),下降幅度達15%。即硫酸陽極氧化處理,對去除包鋁和帶包鋁層的2E12鋁合金的拉伸強度性能影響不大,但斷后伸長率表現出明顯的下降趨勢。
表2 去除包鋁層和帶包鋁層的2E12鋁合金陽極氧化處理前后的拉伸性能結果
2.4 包鋁層和陽極氧化時間對2E12鋁合金疲勞性能的影響
2.4.1 疲勞壽命分析
表3和4分別為去除包鋁層和帶包鋁層的2E12鋁合金經陽極氧化處理不同時間后的疲勞性能測試結果。兩種2E12鋁合金經硫酸陽極氧化處理前后的中值疲勞壽命對比相對值如圖5所示。從表3可以看到,去除包鋁層的2E12鋁合金經陽極氧化不同時間后疲勞壽命下降顯著,僅為未經陽極氧化處理時的30%~36%,但隨氧化時間變化不大。從表4可以看到,帶包鋁層的2E12鋁合金經陽極氧化15,30,45和60 min,疲勞壽命逐漸降低,分別下降到未經陽極氧化處理時疲勞壽命的90%,78%,64%和74%,降低幅度明顯低于去除包鋁層的。
表3 去除包鋁層的2E12鋁合金陽極氧化不同時間后疲勞性能結果
表4 保留包鋁層的2E12鋁合金陽極氧化不同時間后疲勞性能結果
圖5 去除包鋁層和帶包鋁層的2E12鋁合金中值疲勞壽命相對值
硫酸陽極氧化對鋁合金基體疲勞壽命的影響機制主要包含以下兩個過程:(1) 鋁合金在堿腐蝕等前處理以及陽極氧化處理過程中,合金中的第二相合金相顆粒和合金基體中的一些雜質相會發生溶解,在材料表面形成點蝕以及其他缺陷。疲勞加載過程中,外加載荷會促進這些缺陷互相合并融合形成尺寸更大的缺陷。當這些缺陷增大到一定尺寸后,就可以成為疲勞裂紋源。(2) 在硫酸陽極氧化成膜過程中,會在表面及亞表面積累一些殘余拉應力,而陽極氧化膜本身也具有一定的脆性,受到外界疲勞載荷作用時,陽極氧化膜也比較容易發生開裂。初始時,裂紋在陽極氧化膜內擴展,進而向基體內擴展。硫酸陽極氧化工藝中,硫酸電解液也會侵蝕鋁合金基材,形成微觀的孔洞或者裂紋等缺陷。當鋁合金在外界疲勞載荷作用下,基體中的孔洞、裂紋等微觀缺陷,會促進裂紋的萌生和發展,從而導致材料疲勞壽命下降。而對于去除包鋁層的2E12鋁合金,相比于表面包覆一層純鋁的鋁合金,經陽極氧化處理后,由于S和θ等合金相的溶解,會在鋁合金表面生成數量更多、尺寸更大的孔洞以及微裂紋等缺陷,導致疲勞壽命下降的幅度也更大。
2.4.2 疲勞斷口分析
圖6為去除包鋁層和帶包鋁層的2E12鋁合金未經陽極氧化以及陽極氧化15,30,45和60 min后的疲勞試樣斷口形貌。可以看出,兩種鋁合金的疲勞斷口形貌均包括疲勞源、裂紋擴展區和瞬斷區等典型區域。兩種鋁合金未經陽極氧化之前,疲勞斷口裂紋源單一,裂紋起源于試樣的棱角處;經陽極氧化處理后,裂紋均起源于膜層和基體之間的界面,且有多個裂紋源同時起裂,然后在疲勞載荷作用下,裂紋向基體內部擴展,疲勞試樣發生斷裂,疲勞壽命明顯下降。
圖6 去除包鋁層和帶包鋁層的2E12鋁合金陽極氧化不同時間后的斷口形貌
2E12鋁合金中的合金相在陽極氧化過程中會大量溶解,在合金表面產生均勻分布的較大孔洞,膜中也會產生拉應力,這些缺陷在外界疲勞載荷作用下,就會成為裂紋源,進而導致疲勞性能下降。去除包鋁層和帶包鋁層的2E12鋁合金經硫酸陽極氧化處理后,疲勞壽命均明顯下降,去除包鋁層的2E12鋁合金由于陽極氧化后表面孔洞數量更多、尺寸更大,疲勞壽命下降幅度更大。
3 結論
(1) 去除包鋁層和帶包鋁層的2E12鋁合金經硫酸陽極氧化處理不同時間后,表面均能形成具有防護性能的致密陽極氧化膜。帶包鋁層的2E12鋁合金陽極氧化膜生長速度更快,厚度也更大。
(2) 兩種鋁合金表面陽極氧化膜中都存在大量孔洞,且隨著陽極氧化時間延長,尺寸和數量都逐漸增加。由于去除包鋁層的2E12鋁合金基體中含有富Cu第二相,這些第二相在陽極氧化過程中發生溶解,使得膜層中孔洞的數量和尺寸都明顯增加。
(3) 去除包鋁層和帶包鋁層的2E12鋁合金經硫酸陽極氧化處理后,拉伸性能基本保持穩定,但疲勞壽命均明顯下降。陽極氧化處理后,疲勞斷口呈現多個裂紋源的特征,去除包鋁層的合金表面孔洞的數量更多、尺寸更大,疲勞裂紋更易萌生和擴展,疲勞壽命下降幅度更大。
免責聲明:本網站所轉載的文字、圖片與視頻資料版權歸原創作者所有,如果涉及侵權,請第一時間聯系本網刪除。
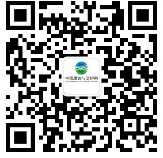
官方微信
《中國腐蝕與防護網電子期刊》征訂啟事
- 投稿聯系:編輯部
- 電話:010-62316606-806
- 郵箱:fsfhzy666@163.com
- 中國腐蝕與防護網官方QQ群:140808414