導(dǎo) 讀
原油中自身含有的、開采、運(yùn)輸過程中加入的以及蒸餾裝置加工過程中形成的腐蝕性物質(zhì)會(huì)對裝置設(shè)備的壽命產(chǎn)生影響,嚴(yán)重時(shí)引發(fā)事故。因此常減壓蒸餾裝置的腐蝕是最為普遍的,也是最為人們所關(guān)注的。加工的原油性質(zhì)不同,所產(chǎn)生的腐蝕性物質(zhì)不同,腐蝕產(chǎn)生的部位及腐蝕類型、機(jī)理不同,需要采用的防護(hù)措施也不同。無論加工哪種類型的原油,在低溫部位普遍存在HCl-H2S-H2O腐蝕,出現(xiàn)在常減壓裝置三頂(初頂、常頂、減頂)冷凝冷卻系統(tǒng)。其中氣液相變部位腐蝕最為嚴(yán)重。高溫部位腐蝕類型主要由加工原油中酸值及硫含量決定,加工高含硫原油時(shí)是高溫硫腐蝕,而加工高含酸原油時(shí)腐蝕以環(huán)烷酸腐蝕為主。高溫腐蝕部位通常發(fā)生在塔器、管線、加熱爐爐管、高溫?fù)Q熱器、高溫機(jī)泵、容器等。加工高含酸原油時(shí)常壓轉(zhuǎn)油線、減壓轉(zhuǎn)油線等流速較高的部位,腐蝕較重。加工高含硫高含酸原油時(shí),還要注意酸硫之間的協(xié)同腐蝕。
常減壓裝置易腐蝕部位及類型
某常減壓蒸餾(下稱常減壓)裝置主要由電脫鹽系統(tǒng)、初餾系統(tǒng)、常壓系統(tǒng)、減壓系統(tǒng)和燃料回收系統(tǒng)等組成。裝置主要工藝流程及易發(fā)生腐蝕類型如下。
裝置腐蝕情況分析
腐蝕檢查:對常壓裝置、減壓裝置兩個(gè)工藝區(qū)內(nèi)的設(shè)備進(jìn)行腐蝕分析,對主要的設(shè)備進(jìn)行外部宏觀檢測、腐蝕產(chǎn)物能譜分析、內(nèi)窺鏡檢測、硬度檢測以及對腐蝕嚴(yán)重的部位進(jìn)行測厚。裝置中主要設(shè)備腐蝕現(xiàn)象如下。
腐蝕原因分析
通過對上述列出的腐蝕現(xiàn)象以及工藝流程進(jìn)行分析,常減壓工藝中存在腐蝕機(jī)理主要有HCl-H2S-H2O腐蝕、高溫硫腐蝕、環(huán)烷酸腐蝕、高溫?zé)煔饬蛩崧饵c(diǎn)腐蝕、保溫層下腐蝕、沖蝕以及高溫氧化。
01 HCl-H2S-H2O腐蝕
在該工藝中,HCl-H2S-H2O腐蝕的位置主要是三塔頂(初餾塔、常壓塔、減壓塔)部分,塔體、部分揮發(fā)線及三塔頂至冷凝系統(tǒng)之間的設(shè)備,和溫度低于150℃的地方。腐蝕介質(zhì)主要是鹽酸、硫化氫和水。由于HCl和H2S沸點(diǎn)較低,因此,會(huì)聚集在分餾塔頂部,遇到蒸汽冷凝水可能會(huì)形成pH值為1~1.3的強(qiáng)酸腐蝕介質(zhì)。一般在氣相部位腐蝕較輕微,液相部位腐蝕比較嚴(yán)重,氣液相變處腐蝕最為嚴(yán)重。對碳鋼來說,腐蝕表現(xiàn)為均勻腐蝕或出現(xiàn)孔蝕;對奧氏體不銹鋼則表現(xiàn)為氯化物應(yīng)力腐蝕開裂。
02 高溫硫和環(huán)烷酸腐蝕
高溫硫腐蝕和環(huán)烷酸腐蝕都屬于高溫腐蝕,當(dāng)溫度處于240~425℃時(shí),可發(fā)生腐蝕,且分子量越低越易發(fā)生。腐蝕的部位主要在初餾塔底部至換熱系統(tǒng)間,常壓塔中部到底部,減壓塔各側(cè)線部位,減壓渣油換熱器,均存在高溫硫和環(huán)烷酸的腐蝕。在高溫條件下,活性硫與金屬能直接反應(yīng),它出現(xiàn)在與物流接觸的各個(gè)部位,表現(xiàn)為均勻腐蝕形貌。高溫硫腐蝕與溫度、流速、硫化物的形態(tài)以及設(shè)備材質(zhì)有關(guān)。溫度升高可促進(jìn)非活性硫分解為活性硫,而且溫度越高腐蝕越嚴(yán)重。當(dāng)溫度高于240℃時(shí),隨溫度升高,硫腐蝕逐漸加劇,當(dāng)達(dá)到350~400℃時(shí),分解出的單質(zhì)硫比H2S腐蝕更劇烈,到430℃時(shí)腐蝕到達(dá)最大值。當(dāng)高溫硫化物剛開始進(jìn)行腐蝕的時(shí)候,金屬表面會(huì)生成一層致密的FeS保護(hù)膜,保護(hù)金屬使腐蝕速率下降。但是,若設(shè)備內(nèi)流速高或在彎頭、三通、變徑等湍流處,金屬保護(hù)膜被沖刷掉,就開始新的腐蝕;若流速更大的時(shí)候,金屬表面根本不能形成保護(hù)膜,腐蝕速率更大。環(huán)烷酸腐蝕通常發(fā)生在操作溫度介于260~400℃工段的設(shè)備中,且產(chǎn)生局部腐蝕。當(dāng)酸值超過1.0mgKOH·g-1,腐蝕更加劇烈。環(huán)烷酸可與金屬直接反應(yīng)生成環(huán)烷酸鐵,且不需要有水的參與。生成的鐵鹽溶于油,不易形成保護(hù)膜,因此,腐蝕后可形成輪廓清晰的蝕坑或流線狀槽紋。若流速較高時(shí),流線狀的槽紋更加明顯。
03 高溫?zé)煔饬蛩崧饵c(diǎn)腐蝕
加熱爐中的燃料油在燃燒過程中生成含有SO2和SO3的高溫?zé)煔猓诩訜釥t的低溫部位,SO2和SO3與空氣中水分共同在露點(diǎn)部位冷凝,產(chǎn)生硫酸露點(diǎn)腐蝕,因此,加熱爐煙道腐蝕嚴(yán)重。
04 保溫層下腐蝕
處于低溫部位的設(shè)備管道容易出現(xiàn)保溫層腐蝕(詳情請點(diǎn)擊這里),當(dāng)設(shè)備處于150℃以下時(shí),容易出現(xiàn)保溫層下的腐蝕。常減壓裝置上易出現(xiàn)保溫層下腐蝕的位置有運(yùn)行在-10~120℃的碳鋼系統(tǒng),有工藝泄露、操作環(huán)境濕度大或酸性蒸汽的區(qū)域,暴露在蒸汽排放口處的設(shè)備,露點(diǎn)以下溫度運(yùn)行的冷設(shè)備等。在腐蝕的部位可以看到金屬表面有大量銹跡,設(shè)備材質(zhì)較脆、粉化、缺少光澤,伴有鼓泡、裂紋等現(xiàn)象。造成保溫層下腐蝕主要有兩方面的因素:
(1)保溫材料中含有氯化物、氟化物和硫化物等有害的腐蝕性成分;
(2)保溫材料多為孔結(jié)構(gòu),有吸附和吸水能力。
防腐策略
在工藝裝置中,腐蝕類型多種多樣,通過腐蝕檢查后,可以結(jié)合以下的防腐策略對設(shè)備的腐蝕情況進(jìn)行監(jiān)管:
①原油調(diào)控
②加強(qiáng)助劑使用工作
③有效控制注水量,改善注水水質(zhì)
④加強(qiáng)表面處理施工質(zhì)量管理
⑤建立腐蝕監(jiān)測體系,加強(qiáng)監(jiān)測數(shù)據(jù)管理
⑥建立腐蝕失效分析案例庫
01 工藝防腐策略
工藝防腐是解決設(shè)備腐蝕的根本方法,是從源頭上降低和控制腐蝕,而且是眾多防護(hù)方法中最為有效的一種。通過合理控制工藝參數(shù),使裝置的整體腐蝕狀況處于可控的范圍之內(nèi)。
首先,加強(qiáng)“一脫三注”技術(shù),即原油脫鹽,揮發(fā)線注氨、注緩蝕劑、注水。電脫鹽是工藝防腐的第一步,通常原油經(jīng)二級電脫鹽后,含鹽量控制在3mg·L-1以下時(shí),才可有效緩解后續(xù)設(shè)備的腐蝕。在常減壓工藝中,建議對每個(gè)塔的每種注入劑采用一臺(tái)泵,方便調(diào)節(jié)注劑量和種類。定期對電脫鹽后的原油和三頂水進(jìn)行采樣分析,來控制電脫鹽的效果。另外,增設(shè)pH探針,對塔頂冷凝水的pH值進(jìn)行檢測,可對中和劑的注入效果進(jìn)行檢測;
其次,由于常減壓裝置中設(shè)備和管道的材料等級較低,對于操作溫度大于220℃的管道加注高溫緩蝕劑。
最后,對于常減壓工藝中“三頂”部位的腐蝕,可通過減少塔頂蒸汽冷凝量來降低鹽酸及其酸性介質(zhì)的含量,從而緩解腐蝕速率,例如,適當(dāng)提高“三頂”部位的溫度,將溫度控制在110℃以上,可有效減少冷凝液的量。
02 設(shè)備防腐策略
設(shè)備防腐主要包括材料防腐、結(jié)構(gòu)防腐和涂料防腐3個(gè)方面。
(1)材料防腐主要就是指材質(zhì)升級,是應(yīng)對高溫腐蝕的主要手段。中石化有關(guān)規(guī)定指出,實(shí)際腐蝕速率大于0.25mm·a-1,就表明選材等級偏低,需要進(jìn)行材料升級。在常減壓工藝中,常壓塔和減壓塔頂高溫部位采用0Cr13Al之類的鐵素體不銹鋼,塔盤或浮閥等內(nèi)部構(gòu)件采用0Cr13;對于實(shí)際操作溫度高于220℃的設(shè)備,可將材質(zhì)升級為Cr5Mo;而為了防止加熱爐對流管露點(diǎn)腐蝕,可選用抗露點(diǎn)腐蝕的ND鋼(09CrCuSb)作爐管;
(2)結(jié)構(gòu)防腐主要是避免應(yīng)力集中,局部過熱或者出現(xiàn)湍流。環(huán)烷酸的腐蝕會(huì)隨著流速的增加而加劇,而且經(jīng)常出現(xiàn)在湍流區(qū)域,因此在改造時(shí)對流速較大的部位應(yīng)采用較大管徑,避免出現(xiàn)湍流的情況。在安裝過程中需將設(shè)備內(nèi)部的焊縫磨平,防止渦流的出現(xiàn)。另外,在彎頭、三通、大小頭、變徑的位置應(yīng)該增加壁厚、貼板加強(qiáng)。
(3)涂料防腐是通過添加防腐層,以隔絕介質(zhì)對金屬材料的腐蝕作用。對于碳鋼換熱器、塔盤、容器等可以采用非晶態(tài)鎳磷鍍層技術(shù),來進(jìn)行防腐。
免責(zé)聲明:本網(wǎng)站所轉(zhuǎn)載的文字、圖片與視頻資料版權(quán)歸原創(chuàng)作者所有,如果涉及侵權(quán),請第一時(shí)間聯(lián)系本網(wǎng)刪除。
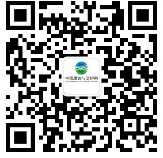
官方微信
《中國腐蝕與防護(hù)網(wǎng)電子期刊》征訂啟事
- 投稿聯(lián)系:編輯部
- 電話:010-62316606-806
- 郵箱:fsfhzy666@163.com
- 中國腐蝕與防護(hù)網(wǎng)官方QQ群:140808414