前 言
石油煉制過程中分餾塔可以將反應后的油氣混合物根據不同的餾程分餾為富氣、汽油、輕柴油、重柴油、回煉油和油漿等餾分,分餾工藝常見于常減壓、催化裂化和焦化等過程。分餾塔頂部循環系統是為了取走分餾塔頂部的過多熱量,通過循環系統的換熱量來控制頂部抽出物料的溫度,從而確保分餾產品的純度合格。分餾塔頂部循環的物料以液相狀態經過換熱和頂循泵加壓后返回分餾塔頂部,該循環系統中的腐蝕越來越被人們所關注。
常減壓是煉油工業的第一個加工裝置,腐蝕問題最嚴重且最復雜。原油逐漸劣質化,電脫鹽前的混合原油氯含量逐漸升高,電脫鹽和脫水的難度逐漸增大,如果超過了電脫鹽裝置的設計要求,脫后原油的鹽質量分數大于3μg/g,就很容易造成常壓塔嚴重腐蝕結垢。
常減壓蒸餾裝置中的腐蝕介質是原油帶來的,主要有氯化物、硫化物、有機酸、有機氯等。對于高硫、高鹽、高酸的原油,常減壓塔各部分的腐蝕主要有3種類型:常壓塔頂及常一線抽出板以上低溫輕油部分發生的是低溫HCl-H2S-H2O型化學和電化學腐蝕;200℃以上柴油及蠟油部分則發生高溫環烷酸化學腐蝕;常減壓塔進料段與塔底則發生高溫硫化學腐蝕和沖蝕。其中腐蝕現象最嚴重的是塔頂的HCl-H2S-H2O型化學和電化學腐蝕。
本研究工作針對常壓分餾塔頂部循環油系統結鹽腐蝕問題設計了一種在線除鹽防腐工藝,并開發了與之配套的成套設備。在此工藝中,關鍵技術難題是如何將油品中微量腐蝕性介質從系統中去除。該技術采用微相分散-順流萃取-油水深度分離的組合脫鹽脫酸方法,通過注水洗脫油品中的腐蝕性介質并完成分離。該成套技術在國內千萬噸級規模煉油廠的常減壓裝置中投入運行,效果良好,明顯降低了分餾塔頂循系統的腐蝕速率。
1、工 藝 流 程
國內某煉油廠常減壓裝置常壓分餾塔頂循環油的抽出量為593.96t/h,抽出溫度為148℃,返塔溫度113℃,采用換熱后的約1/20~1/15循環油油量即30~40t/h進行除鹽脫酸處理,然后再返回分餾塔頂部,以將整個頂循系統腐蝕速率維持在一個較低水平。具體工藝流程見圖1,藍色框線中為改造部分,分餾塔頂循回流油經過冷卻器后,分出30~40t/h頂循回流油進入除鹽成套設備,與2~4t/h凈化水或電脫鹽注水混合,注水在順流徑向萃取器內快速溶解頂循油中的鹽,經油水分離器將溶解了鹽類的廢水除去后的頂循油與另一部分頂循油匯合回流返回塔頂,含油污水進入裝置酸性水系統去下游污水汽提裝置處理。
2、成 套 設 備 及 原 理
分餾塔頂循環油在線除鹽設備主要由湍旋混合器、順流徑向萃取器和油水分離器三部分組成。技術原理如圖2所示,首先通過湍旋混合器將水均勻分散到循環油中,油中的鹽部分溶解到水中,然后經順流徑向萃取器深度捕獲鹽類離子,油水分離器利用粗?;安y強化沉降,快速并高效地實現油水分離,溶水性鹽溶于水中被帶出,達到頂循油在線脫鹽的目的。
降低頂循系統腐蝕的方案中,總是希望抽出的頂循油量和使用的水量最小,從而以最小的能耗實現這些目標,其中關鍵技術是使用高效的液液萃取和分離技術。順流徑向萃取技術是一種緊湊式的高效萃取方式,使用螺旋形混合元件產生高速的旋轉流動,這樣的流動促進了水滴的破碎,并且內部的變徑結構產生多區域小尺寸渦流,強化了徑向混合萃取。由于水滴產生高速自轉,水滴自轉表面的離子交換速度大大提高,宏觀上表現出優秀的萃取能力。
纖維床油水分離使用特殊孔道的纖維層,可以有效地使分散在油中的細小水滴聚結長大,從而增加了油水兩相沉降效率,在同一處理量下,纖維床可以有效地降低沉降空間,縮小油水分離設備的尺寸。液液萃取和液液分離結合點在于水滴尺寸的控制,通過計算除鹽擴散速率來控制萃取后體系的水滴粒徑di,根據di來設計纖維床參數。以最優化方案對分餾塔頂部循環油的無機鹽、酸類物質進行高效脫除。
3、工 業 運 行 結 果 及 標 定
3.1 系統脫鹽效果
該設備運行穩定后,常壓分餾塔頂部循環系統總流量為594t/h,分餾塔頂循分出量為40t/h,注水量為4t/h,頂循分出量約為總循環量的1/15,注水量為頂循油分出量的10%,裝置運行穩定后油水分離器界位分層清晰,切水不帶油,返塔脫鹽油不帶水。現場開工標定持續了9d,每天取一組除鹽裝置進出口頂循油樣進行分析,采用GB/T6532—2012電位滴定法測量進除鹽裝置前后頂循油中鹽含量,這種方法的鹽質量濃度單位為mgNaCl/L,代表了氯類離子在電解池中的電荷遷移量,具體電子遷移量如式(1)表示:Q=c/M。
(1)式中:Q為樣品中含有的負電荷離子物質的濃度,mmol/L;c為測量的鹽質量濃度,mg/L;M為NaCl的摩爾質量,g/mol。
圖3為分餾塔頂循在線除鹽設備的進出口油品中鹽含量及脫鹽效率曲線。由圖3可以看出,設備進口頂循油鹽的初始質量濃度為1.3mgNaCl/L,代表著頂循系統中的油品鹽含量。每一組出口頂循油鹽含量均比入口有一定下降,效率從5%至85%不等。由于設備進出口頂循油不斷地在頂循系統中進行循環,因此鹽含量不盡相同,每一組效率測試結果并不能代表設備每一天的脫鹽效率,但從脫鹽效率上來看經過設備的頂循油中鹽含量均有降低,工藝路線的目的即是通過除鹽設備長期運行將頂循系統中的鹽類不斷帶出系統。
從圖3可以看出,隨著設備的長期運行,頂循油中鹽質量濃度不斷降低,在第9d時降低至0.5mgNaCl/L,雖然在鹽含量較低時設備的脫鹽效率略低,但通過長期運行仍可將常減壓裝置進料帶入的鹽類帶出,控制頂循系統中鹽含量處于較低水平,減緩了腐蝕的發生,可見除鹽設備運行良好。
3.2 系統脫酸效果
圖4所示為進出口頂循油中酸度測試值及脫酸效率曲線,在標定的同時進行了除鹽裝置進出口頂循油酸度的測量。從圖4可以看出,設備投入運行初期酸度值高達40mgKOH/L,經過除鹽設備洗脫后出口頂循油酸度均有降低,脫酸效率從8%至70%不等,和上述鹽含量測試結果類似,每一組效率測試數據并不能代表設備長期運行的結果,但能反映設備運行對于頂循系統長期運行帶來的變化趨勢。
從圖4可見,隨著設備長期運行,頂循系統頂循油酸度不斷降低,標定第9d時降低至18mgKOH/L,頂循油酸度降低是因為其中的腐蝕性介質被洗脫到凈化水中了。對注入除鹽設備的凈化水和油水分離器水相出口切水進行了pH值的測量,分析結果如圖5所示。
從圖5可以看出,入口凈化水平均pH值為9.57,切水的平均pH值為8.05,每一組的切水pH值均較注水pH值約下降1.5個數值,切水pH值的下降側面反映了油品中的酸性腐蝕性介質轉移到了水相中被帶出了頂循系統,降低了分餾塔頂循環系統的腐蝕速率。
3.3 系統腐蝕速率標定
腐蝕探針是目前分餾塔頂循環系統長期運行的主要監測手段,該裝置在頂循系統換熱器入口處設置的腐蝕探針可監測整個頂循系統的腐蝕速率。一般認為控制腐蝕速率在0.2mm/a以下時則表明防腐措施使用得當,腐蝕速率在可接受范圍內。
圖6為該煉油廠在使用在線除鹽裝置前后常壓塔頂循系統腐蝕速率曲線,第一次開工在5月5日,從圖6中可以看出在線除鹽裝置投用前腐蝕速率較高,在0.2~0.6mm/a波動,裝置投用后運行半個月腐蝕速率平穩控制在0.3mm/a上下波動,部分時間段低至0.2mm/a。投用半個月后出現分餾塔內腐蝕產物堵塞湍旋混合器的情況,造成在線除鹽裝置壓力降增大、流量下降,最終停運。
停運后腐蝕速率逐漸上升至0.4mm/a。在切入過濾器進行流程優化后于9月底在線除鹽裝置再次投用,目前常壓塔塔頂循環系統腐蝕速率穩定控制在0.2mm/a以內,處于0.1mm/a上下波動的狀態,說明在線除鹽裝置運行效果良好,有效地將頂循系統內腐蝕性介質和鹽類帶出系統,緩解了塔頂腐蝕,提高裝置運行的安全性和穩定性。
3.4 系統優化及建議
如3.3內容所述,分餾塔頂在線脫鹽脫酸成套技術在投入運行初期,出現了湍旋混合器腐蝕產物堵塞、壓力降增大、流量下降的問題。將湍旋混合器拆卸清洗時發現大量黑色堵塞物,如圖7(a)所示。將堵塞物進行烘干后呈現鮮明的兩種顏色,紅褐色與黃色,見圖7(b)。將兩種顏色堵塞物分別取少量樣品,黃色編號為1號,紅褐色編號為2號,進行粒徑分析及能譜分析。
從能譜分析結果中發現兩種堵塞物主要元素都為Fe和O,分析認為主要成分為鐵及鐵的氧化物,剩下的主要是S元素和C元素,分析認為這兩種元素分別構成FeS和環烷酸腐蝕產物,2號樣品中S元素和C元素含量較1號高出許多,因此1號樣品和2號樣品的顏色差別也許是由于FeS和環烷酸腐蝕產物在總的堵塞物中含量差別造成的。另外1號樣品中還存在少量的金屬元素,比如Al,Si,Ca,Cr,它們形成的氧化物也可能造成1號和2號堵塞物的顏色差異。
將兩種堵塞物分別進行了粒徑分析,分析結果如圖9所示,從粒徑分布曲線中可以發現,兩種堵塞物的粒徑范圍差不多,1號平均粒徑比2號稍大,1號堵塞物粒徑范圍為0.2~50.0μm,分割粒徑D50為8.5μm;2號堵塞物粒徑范圍為0.2~100μm,分割粒徑D50為7.83μm。由于常減壓裝置油品中成分復雜,對在線除鹽裝置造成堵塞,因此在湍旋混合器前增設自動反沖洗過濾器作為分餾塔頂循環系統在線除鹽工藝的預處理工序,開始依據粒徑分析數據選取的過濾器精度為8μm,但在實際應用中發現腐蝕性產物顆粒被油品包裹形成團絮狀,顆粒要明顯大于粒徑分析結果,因此選取自動反沖洗過濾器分離精度為15μm。自從設置了反沖洗過濾器后,該系統運行穩定。
4、結 束 語
常減壓裝置自投用在線除鹽脫酸防腐成套技術后,設備運行安全平穩。在原先塔頂循環系統鹽含量一直超標的情況下持續將頂循油中的酸性腐蝕性介質和鹽類轉移到凈化水中帶出系統,從標定結果來看,在線除鹽設施出口頂循油相較于入口頂循油中鹽含量降低,酸度降低,塔頂循環系統中鹽含量逐漸降低,最終頂循油中鹽含量及酸度分別穩定至1mgNaCl/L,20mgKOH/L以內,分餾塔頂循系統的在線腐蝕探針監測的腐蝕速率穩定控制在0.2mm/a以內。該成套技術設備流程簡單,改造方便,投資較少,能耗低,免去了傳統的注緩蝕劑、中和劑的工序以及洗塔作業產生的輕污油、污水,降低了系統因腐蝕而帶來的材質升級費用,減少了裝置運行成本及設備腐蝕帶來的安全生產問題。
免責聲明:本網站所轉載的文字、圖片與視頻資料版權歸原創作者所有,如果涉及侵權,請第一時間聯系本網刪除。
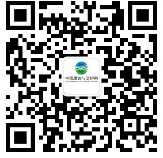
官方微信
《中國腐蝕與防護網電子期刊》征訂啟事
- 投稿聯系:編輯部
- 電話:010-62316606-806
- 郵箱:fsfhzy666@163.com
- 中國腐蝕與防護網官方QQ群:140808414