潔凈鋼是指鋼中五大雜質元素(S、P、H、N、O)含量較低,并且對鋼中非金屬夾雜物進行嚴格控制的鋼種。早期潔凈鋼生產對鋼材性能和潔凈度要求不高,轉爐成為生產潔凈鋼的主要工藝。當時的潔凈鋼技術研發重點是解決頂吹轉爐反應效率低、渣鋼反應偏離平衡和吹煉過程不平穩等技術問題。研發的一些主要技術包括:氧氣底吹轉爐和噴粉技術,各種復吹轉爐以及鐵水脫硫和爐外精煉等。
20世紀70年代以后,由于制造業的快速發展,對鋼材潔凈度要求更加苛刻,如無間隙原子深沖鋼要求[C+N]≤50ppm、軸承鋼要求T.O≤6ppm等,單純依賴轉爐很難達到質量要求。這一時期的研發重點是針對轉爐功能的解析與轉換,形成潔凈鋼生產流程,突破潔凈鋼冶煉的技術極限。主要研發的技術包括:鐵水“三脫”(脫硫、脫硅、脫磷)預處理、轉爐智能吹煉、多功能真空精煉等。
自2000年以來,潔凈鋼生產工藝的研究熱點從單純追求突破潔凈度極限,轉變為降低生產成本、提高生產效率、實現綠色化生產。主要研發成果包括:鋼中最大夾雜物控制、連鑄輕壓下和小壓縮比連鑄,及建立高效低成本潔凈鋼生產平臺等。
1 高效鐵水“三脫”技術
脫磷、脫硫是鋼水提純中最重要的冶金反應。和轉爐相比,鐵水“三脫”(脫硫、脫硅、脫磷)工藝的主要特點是將脫磷、脫硫反應從高溫、高氧位轉移到低溫、低氧位條件下實施,更有利于反應的發生,進而解決了傳統煉鋼中回硫、低碳脫磷和鋼渣過氧化等弊病。
為了開發更經濟、更高效的“三脫”工藝,有專家推薦以下技術:一是根據耦合反應理論,設計在同一反應器內分階段進行脫硅、脫磷和脫硫。二是加強熔池攪拌,開發低FeO渣脫磷工藝(控制渣中TFe≤5%,R=2-2.5),提高脫磷效率達80%以上,半鋼[P]≤0.02%。三是噴粉解決熔池法造渣困難問題,高Ca/O比操作,形成高堿度、低FeO渣深脫硫,使脫硫率≥90%。四是通過靈活調節Ca/O比,精確控制“三脫”反應過程中的氧化還原程度。五是吹煉期采用溢渣工藝,及時排出各反應期生成的爐渣,并實現在線爐渣改質。
2 提高夾雜物控制水平的措施
近年來,業界對夾雜物控制提出更高的要求,在降低夾雜物總量的基礎上,要求嚴格控制夾雜物最大尺寸,大幅提高鋼材的各項性能。
為實現這一目標,應采取以下技術措施:一是用真空碳脫氧代替合金沉淀脫氧,減少脫氧夾雜物;二是抑制或減少精煉中渣鋼反應,避免生成大顆粒變性、卷渣和脫硫夾雜物;三是加強鋼水保護,避免澆鑄中鋼水的二次氧化,從而產生新的夾雜物。
改變脫氧工藝的技術關鍵是提高真空循環脫氣(RH)界面反應速度,促使真空下,碳氧反應接近氣相平衡。具體措施如下:一是擴大真空室表面積;二是真空室吹氬氣,加快鋼液表面的更新速度,增大界面流量;三是采用微氣泡技術(PERM法),在RH精煉前,吹入H2或N2,提高鋼中氣體含量,利用真空脫氣功能,在后期形成大量微氣泡,促進熔池脫碳并有利于夾雜物上浮。
中間包冶金對鋼中夾雜物控制有重要作用,其目標不是進一步提純鋼水,而是嚴格控制澆鑄過程的污染,避免產生二次氧化、卷渣和變性夾雜。具體措施包括:采用大容量中間包,合理設計中間包形狀,避免鋼水形成紊流;加強中間包密封,控制中間包氣氛中的氧含量PO2≤0.1mol%;采用鎮靜開澆工藝,可使鑄坯表層夾雜物富集帶中夾雜物面積率從鎮靜5min開澆的1%下降到鎮靜10min開澆的0.2%;采用無渣澆鑄工藝,如日本山陽特鋼廠生產超純凈軸承鋼,采用無渣澆鑄工藝,可控制鋼中最大夾雜物尺寸≤12μm。
3 建立高效的潔凈鋼生產體系
以日本住友鋼廠1座210t脫磷爐和2座脫碳爐配合2臺KR脫硫站、2臺RH精煉爐和3臺連鑄機,構建的高效快節奏生產平臺為例,其高效快節奏的潔凈鋼生產特點如下:
一是全部產品高品質化。采用100%鐵水“三脫”、100%快節奏生產、100%鋼水真空處理和100%鑄坯熱裝直軋(≥850℃),全部產品雜質總量Σ[S+P+T.O+N+H]≤100ppm。
二是壓縮輔助時間,縮短冶煉周期。通常轉爐輔助時間與吹煉時間之比為1∶1,而雙聯轉爐吹煉時間≤10min,要求壓縮輔助時間≤10min,保證20min周期。加快生產節奏,解決了脫碳爐熱量不足的問題,日產45爐鋼時,冷卻能與傳統轉爐相當,日產55爐鋼時,冷卻能提高7.2%。
三是建立以轉爐為中心的快節奏生產體系。生產周期長于轉爐的KR和RH,采用2臺設備配1臺轉爐;3臺連鑄機同時生產時,連鑄周期為1h,2臺連鑄機同時生產時,連鑄周期為40min。
四是縮短鐵水罐周轉時間,提高周轉次數,鐵水入爐溫度提高46℃。
五是簡化爐外精煉,提高鋼包周轉率,出鋼溫度比傳統轉爐降低30℃,不配置LF爐。
建立高效快節奏的生產方式具有很大的經濟效益:一是提高設備作業率,減少設備臺數,降低管理成本;二是縮短輔助時間,加快鋼包(鐵包)周轉,減少輔助能耗和在線鋼包數量;三是大幅度提高勞動生產率,降低人員成本。
4建立綠色低成本潔凈鋼生產平臺
傳統流程以爐外精煉控制鋼材純凈度,以鐵水“三脫”為基礎的潔凈鋼生產新流程,可以通過以下途徑,降低生產成本:
一是提高反應效率。該流程通過提高渣鋼間磷、硫分配比,抑制鋼渣過氧化,減少脫氧夾雜物以及提高錳資源回收率等措施,降低渣量,減少輔料、鋼鐵料和鐵合金消耗,降低生產成本。
二是實行高效快節奏生產。該流程通過加快生產節奏,提高設備作業率,降低輔助時間能耗和鐵水、鋼水周轉過程溫降等措施,降低生產能耗;通過減少設備臺數簡化備件管理,提高全員勞動生產率,進一步降低生產成本。
三是簡化爐外精煉工序。國內鋼廠普遍采用LF精煉。LF工序能耗高、周期長,渣鋼反應易產生大顆粒夾雜物,國外先進鋼廠已開始抑制LF渣鋼反應甚至取消LF精煉爐。
四是顛覆傳統流程。高品質特鋼須采用電渣(ESR)或真空感應+真空自耗(VAR)等特種冶金和鍛造工藝生產,規模小、成本高。這種狀況已開始改變,如SKF公司通過超低硫冶煉和硫化物控制,使軋材橫、縱向性能偏差從50%降低到10%以下,實現以軋代鍛生產風電軸等產品。日本山陽特殊鋼公司通過改善夾雜物控制工藝,完全消除20μm以上的大型夾雜物,使軸承鋼的疲勞壽命≥108,生產的航空軸承質量已超過采用ESR或VAR工藝生產的產品。
更多關于材料方面、材料腐蝕控制、材料科普等方面的國內外最新動態,我們網站會不斷更新。希望大家一直關注中國腐蝕與防護網http://www.ecorr.org
責任編輯:殷鵬飛
《中國腐蝕與防護網電子期刊》征訂啟事
投稿聯系:編輯部
電話:010-62313558-806
郵箱:fsfhzy666@163.com
中國腐蝕與防護網官方 QQ群:140808414
免責聲明:本網站所轉載的文字、圖片與視頻資料版權歸原創作者所有,如果涉及侵權,請第一時間聯系本網刪除。
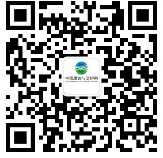
官方微信
《中國腐蝕與防護網電子期刊》征訂啟事
- 投稿聯系:編輯部
- 電話:010-62313558-806
- 郵箱:fsfhzy666@163.com
- 中國腐蝕與防護網官方QQ群:140808414