循環疲勞是工程系統中許多災難性故障的根本原因,著名的例子包括飛機、人造心臟瓣膜、假肢設備、電子封裝、鐵路、橋梁、海上平臺以及常規和核電站。循環加載導致的金屬材料的弱化最終導致斷裂,其應力通常大大低于在單調加載(I)下導致斷裂的必要應力。這樣的失效往往發生在數百萬甚至數十億次循環之后,使預測失效何時發生的能力復雜化發生。
設計安全關鍵元件,使其能夠超過臨界循環次數,需要了解材料在所需循環次數下的疲勞強度。在疲勞強度測量中,在伺服液壓試驗機中,樣品通常在最小和最大應力(Omin, Omax)之間循環,直到失效,頻率接近1hz。在此頻率下,應用100萬個周期需要~278小時,或應用10億個周期需要27.8萬個小時(~32年)。隨著超聲疲勞測試方法的發展(2,3),疲勞測試可以在20 kHz下進行,允許在~14小時內循環10億次。這種加速測試方法能夠在非常高的循環和強度下對更廣泛的材料進行快速的疲勞表征
在高或非常高的循環疲勞狀態下的疲勞強度與金屬材料的固有力學性能之間的相關性,包括屈服強度、極限抗拉強度和硬度,在文獻中得到了廣泛的報道。最有趣的是觀察到疲勞強度隨著屈服強度或極限抗拉強度的增加而增加。然而,繪制歸一化疲勞強度與金屬屈服強度或極限抗拉強度(圖1)顯示,在許多情況下,具有高強度的金屬材料在應力低至屈服強度的25%時因疲勞而失效,表明疲勞效率明顯較低。在微觀結構尺度上連接拉伸、屈服強度和疲勞強度的物理過程和參數尚未完全了解。此外,為什么拉伸強度高的金屬和合金具有如此低的疲勞效率也不清楚。大量的疲勞建模工作,使本構模型與大量的疲勞試驗數據相匹配。
在此,美國伊利諾伊大學厄巴納-香檳分校(UIUC)J. C. Stinville教授團隊等人 本工作通過在循環的最初階段考慮大量單個材料的納米分辨率的循環變形過程,識別出大量面心立方、六方密排和體心立方金屬材料的疲勞強度的物理起源。確定了屈服強度與極限抗拉強度、疲勞強度和早期滑動局部化事件的物理特性之間的定量關系。通過滑動變形的金屬合金的疲勞強度可以通過在第一個加載循環期間滑動局部化的幅度來預測。為眾所周知的經驗疲勞定律提供了物理基礎,并實現了一種快速預測疲勞強度并設計抗疲勞材料的方法。相關研究成果以題“On the origins of fatigue strength in crystalline metallic materials”發表在國際著名期刊Science正刊上。
鏈接:https://www.science.org/doi/10.1126/science.abn0392
▲圖1. 拉伸性能與疲勞強度的關系
利用損傷或疲勞指標參數,大大提高了我們的預測能力。然而,這種模型所依賴的參數并不是所有金屬材料都通用的。疲勞失效是由一系列復雜的過程發生的,包括循環塑性變形、裂紋形核和裂紋擴展到導致斷裂的臨界尺寸。循環變形過程是由晶體缺陷,即所謂的位錯滑移產生的,這些缺陷發展成復雜的結構,如具有梯狀結構的持續滑移帶、變形帶或疲勞剪切帶。疲勞裂紋的成核被認為是一種被稱為循環不可逆現象的結果,在這種現象中,位錯在試樣加載時沿著滑移面滑動,但在卸載或反向加載到壓縮時不會回到原來的位置。這導致了塑性應變的非均勻積累,并伴隨著樣品表面的粗糙化
▲圖2. 表面滑移局部化的定量測量
▲圖3. 疲勞強度作為滑動幅度的函數
▲圖4. 金屬材料的疲勞強度和局部滑移幅度的測量
我們的數據表明,與FCC和HCP金屬相比,BCC金屬傾向于以更均勻的空間方式分布應變。純Nb、純鉭,合金在單調加載過程中產生較低的平均滑移強度。因此,它們表現出非常高的疲勞效率,在某些情況下顯示出高于屈服強度的疲勞強度。HfNbTaTiZr的特殊例子是一個有趣的例外,因為它顯示了最高強度的滑移定位。這種合金中最強烈的滑移痕跡與抑制交叉滑移的特殊晶體取向有關。這些結果表明,對這類合金的晶體織構的控制可能是獲得優異性能的關鍵。對導致高屈服強度BCC合金強烈局部化的位錯機制的深入物理理解也可能為這類材料中的合金設計提供指導。
▲圖5. 體心立方金屬的疲勞和局部化
我們觀察到在第一個周期發展的滑移局部化振幅和材料的疲勞強度之間的線性關系。對于因滑移而變形的材料,我們已經直接量化了滑移幅度、不可逆性和疲勞壽命之間的相互關系。我們的觀察表明,在第一個循環中發生的塑性局部化自然地反映了材料循環不可逆的傾向。我們的分析還捕獲了fcc和hcp材料與bcc相比行為的整體差異,以及bcc合金中更均勻變形的趨勢。滑移分析對于識別具有異常行為的合金也非常有用,如bcc多主元合金HfNbTaTiZr,并為尋找抗疲勞合金提供了一種不同的方法。4這些結果表明,控制這類合金的晶體學織構對于獲得優異的性能可能是至關重要的。對在高屈服強度bcc合金中導致強烈局部化的位錯機制更深入的物理理解也可以為這類材料中合金的設計提供指導。
免責聲明:本網站所轉載的文字、圖片與視頻資料版權歸原創作者所有,如果涉及侵權,請第一時間聯系本網刪除。
相關文章
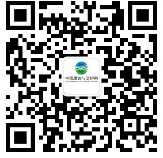
官方微信
《腐蝕與防護網電子期刊》征訂啟事
- 投稿聯系:編輯部
- 電話:010-62316606-806
- 郵箱:fsfhzy666@163.com
- 腐蝕與防護網官方QQ群:140808414
點擊排行
PPT新聞
“海洋金屬”——鈦合金在艦船的
點擊數:8178
腐蝕與“海上絲綢之路”
點擊數:6496