熱塑性復(fù)合材料是什么技術(shù)?
熱塑性復(fù)合材料是以玻璃纖維、碳纖維等增強(qiáng)各種熱塑性樹脂所形成的復(fù)合材料,因具有韌性、耐蝕性和抗疲勞性高,成形工藝簡單、周期短,材料利用率高,預(yù)浸料存放環(huán)境與時(shí)間無限制等優(yōu)異性能而得到快速發(fā)展,并逐漸進(jìn)入航空制造領(lǐng)域.目前,熱塑性復(fù)合材料正在加速進(jìn)入民機(jī)主承力結(jié)構(gòu),這項(xiàng)技術(shù)是軍民通用的,例如可用于軍用運(yùn)輸機(jī).
為什么值得關(guān)注?
比起以環(huán)氧、雙馬等熱固性樹脂所形成的熱固性復(fù)合材料來說,熱塑性復(fù)合材料具備其所沒有的高剛度、低加工成本和再加工能力,擁有良好的阻燃、低煙和無毒性能,固化周期極短,且其成形過程不依賴熱壓罐.這些固有屬性使其成為一種天生的航空結(jié)構(gòu)材料,并且在民機(jī)應(yīng)用上擁有巨大的潛質(zhì),甚至可能在未來為航空復(fù)合材料制造帶來一場熱塑性革命.
空客A380熱塑性機(jī)翼前緣
熱塑性復(fù)合材料(TPC)在民機(jī)應(yīng)用上的巨大潛質(zhì),使得民機(jī)制造商一直非常關(guān)注該材料在民機(jī)主承力構(gòu)件上的應(yīng)用,并開展了眾多研究,研究的重點(diǎn)是主承力構(gòu)件的先進(jìn)制造工藝.這其中,歐洲尤其是荷蘭的貢獻(xiàn)不可小視,歐盟框架研究計(jì)劃中的"熱塑性經(jīng)濟(jì)可承受性航空主結(jié)構(gòu)"(TAPAS)項(xiàng)目在2014年進(jìn)入第6個(gè)年頭,依托荷蘭TPC技術(shù),項(xiàng)目產(chǎn)生了大量成果;波音也與荷蘭TenCate先進(jìn)復(fù)材公司、斯托克?福克公司等建立了熱塑性復(fù)合材料研究中心.
"熱塑性經(jīng)濟(jì)可承受性航空主結(jié)構(gòu)"項(xiàng)目于2009年啟動(dòng),成員包括空客、荷蘭福克航空結(jié)構(gòu)公司、TenCate先進(jìn)復(fù)材公司、荷蘭國家航空實(shí)驗(yàn)室(NLR)等.項(xiàng)目旨在為空客公司開發(fā)TPC平翼扭矩盒和尾翼結(jié)構(gòu),進(jìn)一步增加TPC在當(dāng)前和未來飛機(jī)上的應(yīng)用比例,如A320neo.項(xiàng)目分為兩個(gè)階段,在2017年完成 ,目標(biāo)是兩個(gè)構(gòu)件的材料、制造工藝、設(shè)計(jì)概念和模具設(shè)備達(dá)到技術(shù)成熟度分別達(dá)到4級(jí)和6級(jí).技術(shù)難點(diǎn)包括:開發(fā)和驗(yàn)證適合的材料,"對(duì)接接頭"連接,制造技術(shù),如纖維焊接、壓力成形和纖維鋪放.
福克公司熱塑性扭矩盒驗(yàn)證件
項(xiàng)目第一階段于2013年完成,采用碳纖維/PEKK材料開發(fā)主承力結(jié)構(gòu),項(xiàng)目制造的TPC平尾扭矩盒和機(jī)身驗(yàn)證件分別達(dá)到了技術(shù)成熟度3級(jí)和5級(jí).扭矩盒制造上,由于TPC固有的韌性能更好地阻止裂紋擴(kuò)展,能夠?qū)⒚善ぴO(shè)計(jì)得更薄,因此與熱固性復(fù)合材料構(gòu)件相比,該扭矩盒減重10%.機(jī)身加強(qiáng)筋制造上,由于采用了TPC材料,從數(shù)控切割、機(jī)器人鋪放到真空預(yù)固化、自動(dòng)運(yùn)輸以及壓力成形的整個(gè)制造過程僅需15min.項(xiàng)目的第二階段于2014年初開始,將面向A320neo這樣的單通道客機(jī),繼續(xù)提升TPC扭矩盒和機(jī)身的技術(shù)成熟度,使其獲得市場的關(guān)注.
福克航空結(jié)構(gòu)公司在TAPAS項(xiàng)目之外還開發(fā)了幾個(gè)驗(yàn)證件:TPC帶筋翼面壁板、TPC正弦梁、TPC帶筋機(jī)身壁板,并在2014年進(jìn)行了展示.其中TPC帶筋翼面壁板比碳纖維/環(huán)氧材料減少了15%-30%的成本;正弦梁結(jié)構(gòu)比簡單的I型梁具備更高硬度和抗彎性,而熱固性復(fù)合材料難以快速、經(jīng)濟(jì)地制造這樣的結(jié)構(gòu).
福克公司熱塑性機(jī)身壁板驗(yàn)證件
此外,包括龐巴迪、貝爾直升機(jī)和普惠加拿大等企業(yè)、大學(xué)和政府組織的加拿大魁北克航空研究與創(chuàng)新聯(lián)盟(CRIAQ)完成了兩個(gè)TPC結(jié)構(gòu)的開發(fā)項(xiàng)目,其中包括1.2m長的直升機(jī)TPC尾梁.阿古斯塔?韋斯特蘭AW169直升機(jī)的平尾采用了碳纖維/PPS材料 ,比常規(guī)熱固性復(fù)合材料的設(shè)計(jì)輕了15%,該平尾外形長3m,弦長0.62m,厚0.15m,成為AW169的一大亮點(diǎn).
盡管存在原材料成本高、鋪放工藝緩慢、預(yù)浸料粘性問題等挑戰(zhàn),但熱塑性復(fù)合材料巨大的應(yīng)用潛力還是會(huì)驅(qū)使航空制造商將更多的部件設(shè)計(jì)為熱塑性結(jié)構(gòu),相關(guān)的研究也還將持續(xù)不斷地產(chǎn)出新成果,這都將進(jìn)一步提升熱塑性復(fù)合材料在民機(jī)上的應(yīng)用比例.也許,熱塑性復(fù)合材料就像低溫固化熱固性復(fù)合材料一樣,將曲折但堅(jiān)定的發(fā)展,并在未來由量變轉(zhuǎn)為質(zhì)變,攻克大型民機(jī)的主承力結(jié)構(gòu),實(shí)現(xiàn)廣泛而深層次的應(yīng)用.
責(zé)任編輯:周婭
《中國腐蝕與防護(hù)網(wǎng)電子期刊》征訂啟事
投稿聯(lián)系:編輯部
電話:010-62313558-801
郵箱:ecorr_org@163.com
中國腐蝕與防護(hù)網(wǎng)官方 QQ群:140808414
-
標(biāo)簽: 熱塑性復(fù)合材料, 航空, 碳纖維, 玻璃纖維, 耐腐蝕性
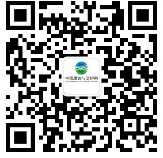
官方微信
《中國腐蝕與防護(hù)網(wǎng)電子期刊》征訂啟事
- 投稿聯(lián)系:編輯部
- 電話:010-62313558-806
- 郵箱:fsfhzy666@163.com
- 中國腐蝕與防護(hù)網(wǎng)官方QQ群:140808414