鎳基高溫合金以其出色的高溫性能而聞名,廣泛應(yīng)用于先進(jìn)飛機(jī)發(fā)動(dòng)機(jī)的渦輪葉片和導(dǎo)向葉片的制造。傳統(tǒng)上,這些高溫合金是通過(guò)鑄造、粉末冶金或鍛造方法生產(chǎn)的,這些方法在制造復(fù)雜零件方面存在局限。傳統(tǒng)工藝中復(fù)雜的步驟和材料浪費(fèi)阻礙了高溫合金的進(jìn)一步發(fā)展。增材制造(AM)是一種新興技術(shù),其中三維零件在計(jì)算機(jī)控制下逐層制造,提供接近凈成形的生產(chǎn)。這種創(chuàng)新方法有望通過(guò)提供更高的精度、增強(qiáng)的材料利用率和前所未有的設(shè)計(jì)靈活性來(lái)解決當(dāng)前的挑戰(zhàn)。在金屬基材料逐層打印過(guò)程中,局部高能輸入和重復(fù)加熱導(dǎo)致復(fù)雜的熱歷史和缺陷的形成,例如裂紋和孔隙。這一問(wèn)題在鎳基高溫合金的增材制造中尤為顯著,因此阻礙了它們的廣泛應(yīng)用。主要的影響因素包括:合金的寬凝固區(qū)間,固溶強(qiáng)化的難熔金屬元素(W、Mo、Cr和Co)和沉淀強(qiáng)化元素(Al、Ti、Ta和Nb)的添加擴(kuò)大了凝固區(qū)間;元素偏聚和液化源的形成,在凝固過(guò)程中元素(如Al、Ti、Ta、C和Hf)的局部富集引起溶質(zhì)偏聚,降低局部熔點(diǎn)溫度,并導(dǎo)致在固態(tài)枝晶之間形成低熔點(diǎn)相,這可能導(dǎo)致打印過(guò)程中裂紋的形成;內(nèi)部殘余應(yīng)力,包括熱應(yīng)力和相變應(yīng)力,兩者都導(dǎo)致微觀結(jié)構(gòu)的不穩(wěn)定。高水平的殘余熱應(yīng)力可能會(huì)破裂高角度晶界或液膜,形成裂紋,而相變應(yīng)力是由于在循環(huán)固有加熱過(guò)程中γ'相的析出和生長(zhǎng)引起的。γ'相的快速和大規(guī)模析出可能導(dǎo)致顯著的應(yīng)力集中,導(dǎo)致γ相和γ'相之間的裂紋。因此,可焊合金通常具有較低程度的合金化并且缺乏高溫強(qiáng)化的γ′相。這些增材制造的高溫合金通常被應(yīng)用于中低溫環(huán)境中,例如IN718和IN625等材料。相反,傳統(tǒng)的高性能工程高溫合金,如第二代單晶高溫合金CMSX-4和CM247LC,其在增材制造過(guò)程中容易出現(xiàn)裂紋,這歸因于其高的強(qiáng)化相γ′的體積分?jǐn)?shù)(>60%)和眾多難熔金屬元素的存在。盡管對(duì)裂紋形成機(jī)理進(jìn)行了廣泛的研究,但完全控制裂紋的形成仍然是困難的。僅僅通過(guò)工藝優(yōu)化無(wú)法完全消除復(fù)雜結(jié)構(gòu)的微缺陷,這凸顯了為增材制造量身定制新合金設(shè)計(jì)的迫切需要。高γ′相體積分?jǐn)?shù)合金設(shè)計(jì)挑戰(zhàn)近年來(lái),各種用于增材制造合金的成分設(shè)計(jì)方法不斷涌現(xiàn)。有研究提出了一種基于計(jì)算建模的合金設(shè)計(jì)方法(ABD),并成功開(kāi)發(fā)出兩種含有中等γ′相體積分?jǐn)?shù)(20%–30%)的合金。另外,另一項(xiàng)研究通過(guò)一系列計(jì)算設(shè)計(jì)了一種抗缺陷的Co-Ni高溫合金SB-CoNi-10,基于Co-Al-W合金體系,實(shí)現(xiàn)了高γ′相體積分?jǐn)?shù)(約70%)。這些成功的設(shè)計(jì)和優(yōu)化工作凸顯了元素調(diào)控產(chǎn)生新型高溫合金等級(jí)的能力。然而,以往用于設(shè)計(jì)增材制造鎳基高溫合金的新合金的方法主要集中在獲得無(wú)裂紋的合金,其γ′相體積分?jǐn)?shù)中等偏低或易受γ′結(jié)構(gòu)惡化的影響,未能充分滿足渦輪葉片制備的高溫力學(xué)要求。為了填補(bǔ)這一空白并開(kāi)發(fā)適用于渦輪葉片制備的合金,必須在高γ′相體積分?jǐn)?shù)和低裂紋敏感性之間取得平衡。這種雙重考慮確保了優(yōu)秀的機(jī)械性能和成形性。本研究介紹了一種新穎的合金設(shè)計(jì)方法,通過(guò)控制γ′形成元素的組成,包括Al、Ti和Ta,特別關(guān)注Ta/Al比值,利用d-電子合金理論和Thermal-Calc(使用TCNI10數(shù)據(jù)庫(kù))。調(diào)整γ′形成元素的含量和Ta/Al比值導(dǎo)致了狹窄的凝固區(qū)間、最小的溶質(zhì)偏聚以及γ′相的緩慢析出。這種調(diào)整有效地減輕了晚期凝固或相變過(guò)程中的應(yīng)力集中,從而降低了裂紋敏感性。設(shè)計(jì)先進(jìn)的增材制造高溫合金的主要原則是在最小化裂紋敏感性的同時(shí)實(shí)現(xiàn)高γ′相體積分?jǐn)?shù)。為了獲得豐富的γ′相含量,選擇了Al、Ti和Ta等元素。基于其分子式(Ni3Al, L12),Al作為關(guān)鍵的γ′相形成元素。Ta由于具有較大的原子半徑,有助于調(diào)節(jié)γ′-析出物的尺寸和形態(tài),并加強(qiáng)它們的性能。添加Ti旨在確保抵抗熱腐蝕,并保持足夠的γ′含量。值得注意的是,由于Nb具有形成Laves相的高傾向,因此未被選擇。因此,目標(biāo)合金中的γ′相組成被表示為Ni3(Al, Ti, Ta)。這一新穎的程序涉及在包括Al、Ti和Ta元素的合金成分設(shè)計(jì)空間中,根據(jù)預(yù)先確定的γ′相體積分?jǐn)?shù)和裂紋因素的篩選條件,縮小選擇范圍。隨后,進(jìn)一步確定了新合金的潛在成分。Al、Ti和Ta的設(shè)計(jì)基于合金7–9 W-7–9Cr-7–9Co-1–3Mo-0.01 C-0.015B-Bal.Ni(重量%)。本研究采用了計(jì)算密集型的熱力學(xué)建模方法以及傳統(tǒng)的合金設(shè)計(jì)方法來(lái)理性確定合金成分。在設(shè)計(jì)階段評(píng)估了超過(guò)103種合金,包括傳統(tǒng)變種。該過(guò)程的進(jìn)一步詳細(xì)說(shuō)明如圖1所示。在新合金中最大化γ′相的含量對(duì)于在高溫下實(shí)現(xiàn)優(yōu)越的機(jī)械性能至關(guān)重要。具有立方形狀和適當(dāng)尺寸的強(qiáng)化γ′相至關(guān)重要。在γ′相中應(yīng)用固溶強(qiáng)化和析出強(qiáng)化機(jī)制有效地阻礙了位錯(cuò)運(yùn)動(dòng),并有助于形成穩(wěn)定的界面結(jié)構(gòu),如位錯(cuò)網(wǎng)絡(luò)。這些改進(jìn)顯著增強(qiáng)了合金抵抗損傷和預(yù)防失效的能力。本研究考慮了三種方法來(lái)降低裂紋敏感性。首先,采用狹窄的凝固區(qū)間來(lái)減輕與凝固相關(guān)的裂紋。合金的凝固區(qū)間是通過(guò)使用TCNI10數(shù)據(jù)庫(kù)進(jìn)行非平衡凝固的Scheil分析確定的(假設(shè)沒(méi)有背擴(kuò)散)。其次,參考Prager-Shira焊接性圖評(píng)估了低應(yīng)變時(shí)效(SAC)優(yōu)點(diǎn)指數(shù),用于評(píng)估熱循環(huán)和固態(tài)后處理過(guò)程中的裂紋情況。最后,在最終液態(tài)凝固過(guò)程中,最小化元素偏聚增強(qiáng)了抵抗液膜相關(guān)裂紋的能力。值得注意的是,由于其無(wú)法準(zhǔn)確反映不同相(如γ基體、γ′相和碳化物)中的偏聚行為,因此未使用固態(tài)中的元素含量。此外,利用d-電子合金理論評(píng)估了微觀結(jié)構(gòu)的穩(wěn)定性,以預(yù)防形成密排結(jié)構(gòu)(TCP)相。最終的合金成分是通過(guò)對(duì)所有計(jì)算因素進(jìn)行全面分析確定的。圖2. 通過(guò)新方法獲得的高溫合金的合金設(shè)計(jì)空間和相關(guān)結(jié)果,包括用于驗(yàn)證的幾種傳統(tǒng)合金。(a和b)顯示了在900°C下,Al、Ta和Ti含量與γ’相含量的關(guān)系趨勢(shì),通過(guò)Thermal-Calc(使用TCNI10數(shù)據(jù)庫(kù))計(jì)算得出。(c)展示了Scheil凍結(jié)范圍與γ’相含量之間的關(guān)系。(d)說(shuō)明了在1350°C下,隨著Ta含量的變化,元素在最終液態(tài)中的偏聚行為。(e和f)展示了與γ’相含量相關(guān)的焊接性圖和應(yīng)變時(shí)效裂紋優(yōu)點(diǎn)指數(shù)限制的設(shè)計(jì)空間。在設(shè)計(jì)空間內(nèi)合金成分的選擇以及相應(yīng)的計(jì)算結(jié)果如圖2所示。首先,基于達(dá)到40%–60%的γ′相體積分?jǐn)?shù)的設(shè)計(jì)目標(biāo),確定了Al、Ti和Ta的成分范圍。從圖2(a)和2(b)的分析中可以看出,γ′相含量與Al呈強(qiáng)烈的正相關(guān),而Ta和Ti則起到了補(bǔ)充作用。值得注意的是,與Ta相比,Al在形成γ′相方面表現(xiàn)出更高的效率,這表明當(dāng)Al和Ti含量降低時(shí),需要更高的Ta含量才能獲得大量的γ′相。利用Ta和Al對(duì)γ′相含量的相反影響趨勢(shì),即高Ta/Al比,證明了在控制γ′相水平方面的高效性。受控的γ′含量不僅通過(guò)降低相變應(yīng)力調(diào)節(jié)了固態(tài)裂紋,而且增強(qiáng)了合金的性能。預(yù)計(jì)高含量的Ta和γ′相將增強(qiáng)機(jī)械性能,這也得到了輔助資料中的統(tǒng)計(jì)結(jié)果的支持。因此,高Ta/Al比是新的合金設(shè)計(jì)方法的一個(gè)關(guān)鍵前提。此外,由于Ti對(duì)結(jié)構(gòu)穩(wěn)定性的不利影響,逐漸在更高代的鑄造合金中減少或消除。然而,由于其對(duì)抗熱腐蝕的有益影響以及在合金中保證足夠的γ′含量,仍然納入了少量的Ti。圖2(c)說(shuō)明了Scheil凝固區(qū)間與γ′相含量之間的關(guān)系。很明顯,靠近頂部的合金表現(xiàn)出更高的裂紋敏感性。凝固區(qū)間為300K,介于不可打印的合金IN939(320K)和易于打印的合金IN718(255K)之間,被選為低/高裂紋敏感性的邊界值。許多可打印的合金的凝固區(qū)間接近或低于這個(gè)邊界值,因此,盡管最大限度地增加γ′相的含量,設(shè)計(jì)目標(biāo)是盡可能地使凝固區(qū)間與邊界值(300K)接近。在圖2(d)中,隨著鉭含量的增加,最終凝固過(guò)程中元素含量的變化被描述了出來(lái)。隨著鉭含量的增加,鈦、碳、硼和鉬等元素明顯減少,而鎢、鈷、鉻和鋁等元素略有增加。具體來(lái)說(shuō),高鉭/鋁比,以高鉭含量和低鋁含量為特征,可以減少最終凝固過(guò)程中的元素偏聚。這種減少有利于減輕低熔點(diǎn)相的發(fā)生,并有效調(diào)節(jié)凝固/再熔相關(guān)的裂紋。關(guān)于高應(yīng)變時(shí)效裂紋,圖2(e)和2(f)描述了焊接社區(qū)提出的焊接性、SAC優(yōu)點(diǎn)指數(shù)和預(yù)期的γ′相體積分?jǐn)?shù)之間的權(quán)衡關(guān)系。隨著γ′相含量的增加,裂紋風(fēng)險(xiǎn)也增加。圖2(e)中靠近邊界的合金組成更有利于保留更高比例的γ′相。選擇了最大SAC優(yōu)點(diǎn)指數(shù)為4.7,介于報(bào)道的可焊合金ABD-900AM(3.9)和不可焊合金IN792(5.1)之間。此外,綜合考慮還包括確保Ti + Al < 6 wt%,金屬d級(jí)別值Md < 0.99,以及電子空位數(shù)NV. < 2.44。總體而言,協(xié)同增強(qiáng)機(jī)械性能和成形性的主要設(shè)計(jì)理念的特點(diǎn)是高Ta/Al比,并且明顯依賴于邊界成分(例如圖2(c)中低/高裂紋敏感性的凝固區(qū)間附近區(qū)域或圖2(f)中可焊/不可焊合金的SAC優(yōu)點(diǎn)指數(shù)附近區(qū)域)。這種方法通過(guò)調(diào)整Ta/Al比,有效控制和加強(qiáng)γ′相,抑制在枝晶間形成低熔點(diǎn)相,縮小合金的凝固區(qū)間,最終降低其裂紋敏感性,同時(shí)改善其機(jī)械性能。基于這一分析,成功開(kāi)發(fā)了一種名為ZGH451-1的無(wú)裂紋合金,其含有高的γ′含量,并采用定向能量沉積(DED)進(jìn)行制造。此外,為驗(yàn)證這種方法的合理性和可行性,還在相同條件下分析了具有不同Ta/Al比的另外兩種合金,ZGH451-2和ZGH451-3。實(shí)驗(yàn)過(guò)程不再展開(kāi),直接上結(jié)論:1、提出了一種基于高Ta/Al比和強(qiáng)邊界成分依賴性的新的增材制造鎳基高溫合金設(shè)計(jì)方法,考慮了合金組成、缺陷控制和機(jī)械性能,以克服制造可行性和材料性能之間的困難。采用計(jì)算密集型的熱力學(xué)建模,成功從合金設(shè)計(jì)空間中分離出了一種名為ZGH451–1的無(wú)裂紋高γ′相含量的新合金,在各種條件下展現(xiàn)出優(yōu)異的機(jī)械性能。2、在兩種合金ZGH451–2和ZGH451–3中,由于其設(shè)計(jì)與新方法相去甚遠(yuǎn),降低了Ta/Al比,出現(xiàn)了各種類型的裂紋,包括凝固裂紋、滲溶裂紋和固態(tài)裂紋,每種合金的裂紋分布存在一些差異。兩種合金都明顯出現(xiàn)凝固裂紋和滲溶裂紋的情況,但只有ZGH451–3中出現(xiàn)了固態(tài)裂紋,因?yàn)槠?/span>Ta/Al比最低。而在首選合金中,樣品的所有位置都沒(méi)有觀察到任何形式的裂紋。3、對(duì)新設(shè)計(jì)的合金調(diào)控裂紋的多種有利因素進(jìn)行了充分驗(yàn)證。首先,通過(guò)合金成分設(shè)計(jì)導(dǎo)致的更窄的Scheil凝固區(qū)間和較低的SCI值有效優(yōu)化了凝固行為,降低了凝固裂紋的敏感性。其次,高Ta/Al比降低了合金的有效擴(kuò)散性,并抑制了間隔元素的偏聚,消除了低熔點(diǎn)(γ+γ′)共晶池,從而消除了滲溶裂紋。最后,由于高Ta/Al比造成的γ′相冷卻速率最低和足夠的變形抵抗,提高了抵抗固態(tài)裂紋的能力。同時(shí),強(qiáng)烈的邊界成分依賴性最大化了上述效應(yīng),并嚴(yán)格限制了γ′含量,確保了更低的裂紋敏感性。4、廣泛的性能比較(包括拉伸和蠕變?cè)囼?yàn))表明,新設(shè)計(jì)的合金具有優(yōu)異的性能和較高的加工性。DED的內(nèi)在熱處理使得構(gòu)件的結(jié)構(gòu)處于未完全熱處理狀態(tài),并具有一定比例的γ′相,因此合金ZGH451–1的機(jī)械性能優(yōu)于大多數(shù)已報(bào)告的增材制造合金和部分熱處理的一/二代鎳基單晶高溫合金。5、這種新的合金設(shè)計(jì)方法確實(shí)可以開(kāi)發(fā)出具有高γ′相含量和少量裂紋的新型高溫合金等級(jí),這可以彌補(bǔ)增材制造合金缺乏高溫性能的問(wèn)題,或解決目前它們打印性能差的問(wèn)題,實(shí)現(xiàn)了兩者的協(xié)同優(yōu)化。此外,ZGH451–1優(yōu)異的微觀結(jié)構(gòu)穩(wěn)定性表明,常規(guī)的合金設(shè)計(jì)方法部分適用于設(shè)計(jì)增材制造合金,例如d-電子合金理論。
DOI:https://doi.org/10.1016/j.addma.2024.104098
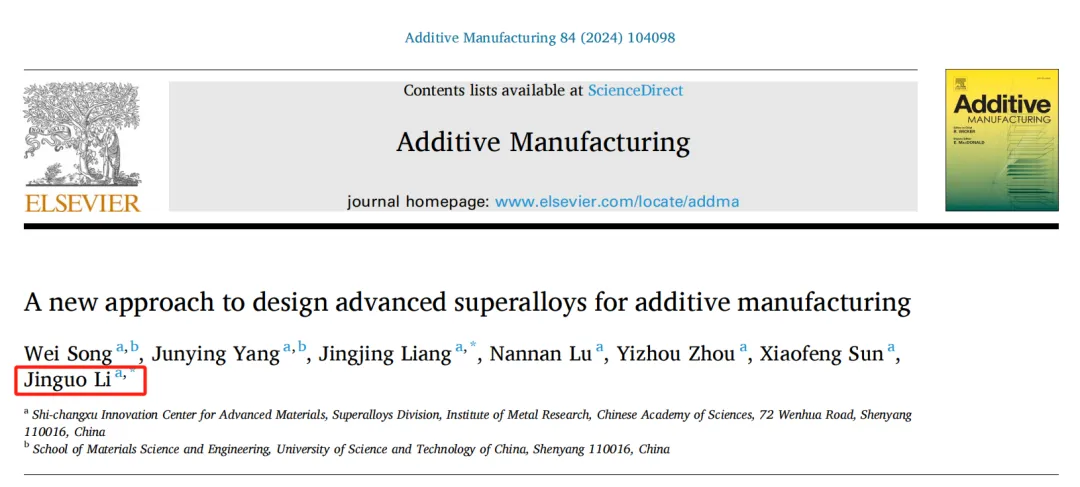
主要圖文
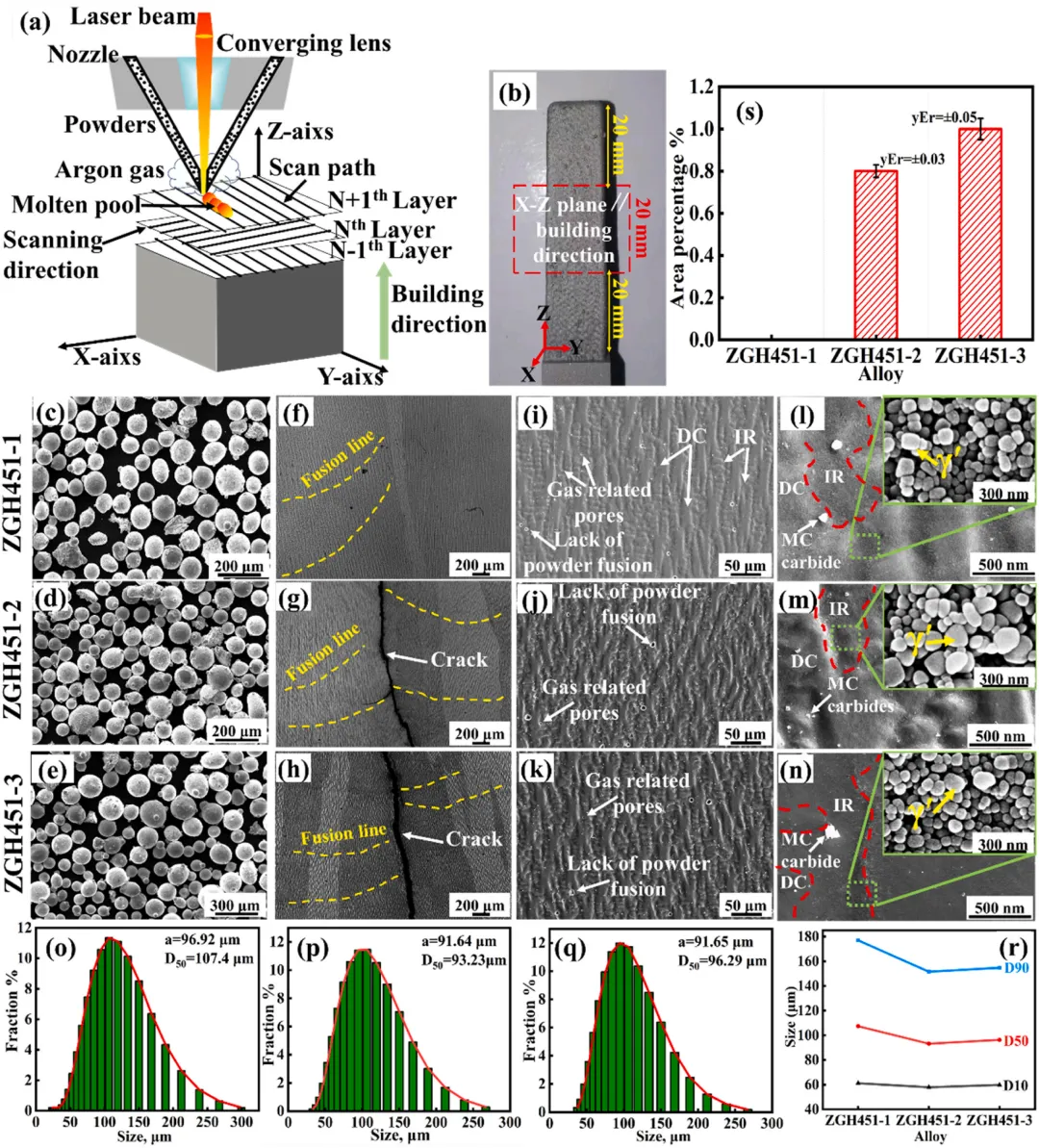
圖3. 對(duì)ZGH451-1、ZGH451-2和ZGH451-3合金的構(gòu)建微觀結(jié)構(gòu)和相應(yīng)的粉末的整體檢查和分析,觀察到的結(jié)構(gòu)平行于構(gòu)建方向(X-Z平面)。(a,b)顯示了DED過(guò)程的示意圖和每個(gè)立方體的XZ-平面切割位置示意圖。(c-e)為粉末的掃描電鏡圖像。(f-h)顯示了X-Z平面典型柱狀晶粒結(jié)構(gòu)的金相顯微鏡圖像,(i-k)為這些柱狀晶的掃描電鏡圖像。(l-n)為掃描電鏡放大的柱狀晶圖像,展示了DC、IR、微小γ'相和MC碳化物。(o-r)展示了三種合金粉末的大小和形態(tài)的一致關(guān)系。(s)顯示了根據(jù)面積百分比估計(jì)的合金裂紋程度。

圖4. 在ZGH451-2 (a-c) 和 ZGH451-3 (d-f) 合金的構(gòu)建微觀結(jié)構(gòu)中觀察到的凝固裂紋,顯示了典型特征:主要枝晶臂、收縮空洞以及位于IR中。
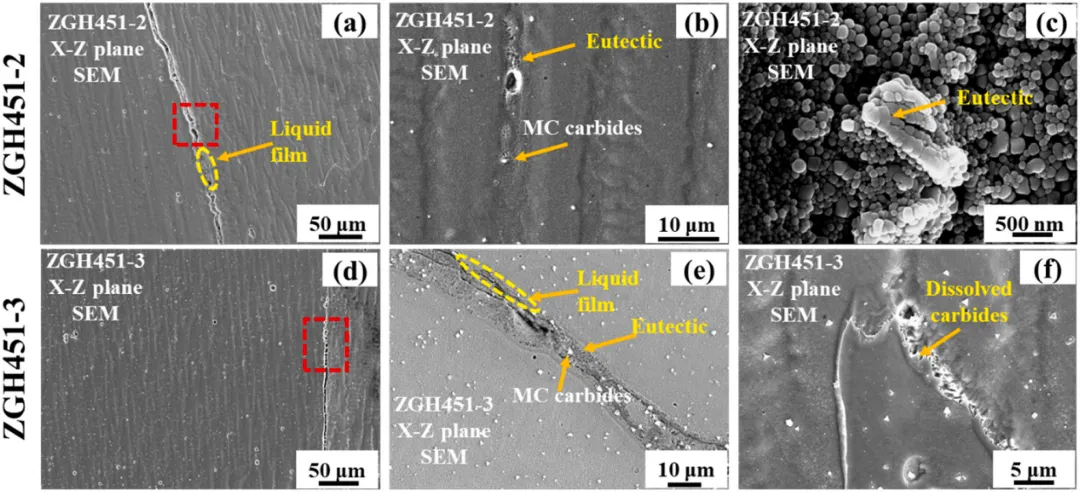
圖5. 在ZGH451-2 (a-c) 和 ZGH451-3 (d-f) 合金的構(gòu)建微觀結(jié)構(gòu)中觀察到的滲溶裂紋。
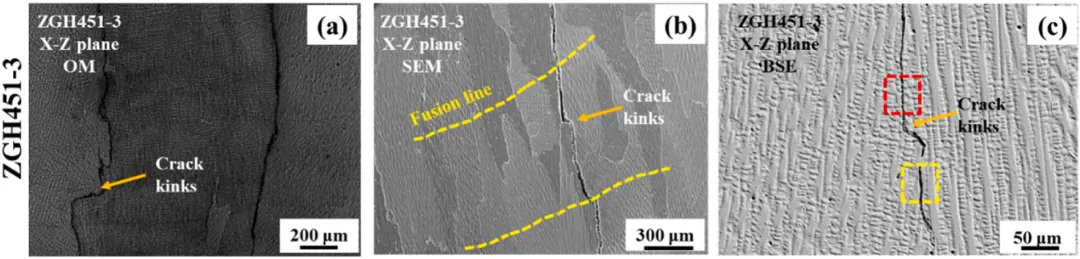
圖6. 在ZGH451-3合金的構(gòu)建微觀結(jié)構(gòu)中觀察到的固態(tài)裂紋。
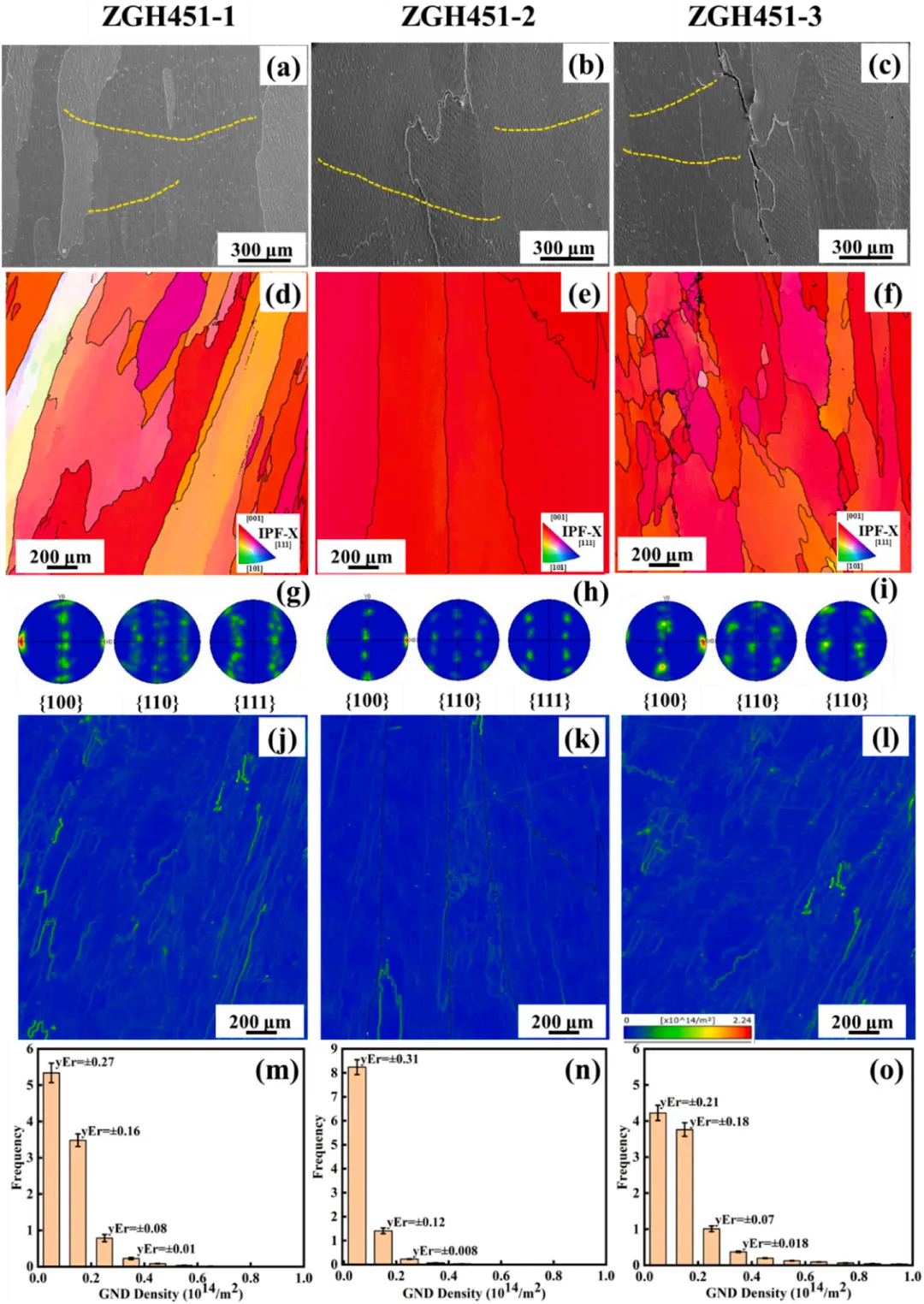
圖7. 三種合金(構(gòu)建狀態(tài))在X-Z平面的SEM、EBSD-IPF(X軸)、極圖和位錯(cuò)密度。(a-c)顯示了柱狀晶的SEM圖像。(d-f)展示了沿構(gòu)建方向的IPF。(g-i)給出了{(lán)1 0 0}、{1 1 0}和{1 1 1}極的晶粒取向分布圖。(j-l)展示了合金體積部分的位錯(cuò)密度分布,(m-o)是展示了具體數(shù)值的直方圖。
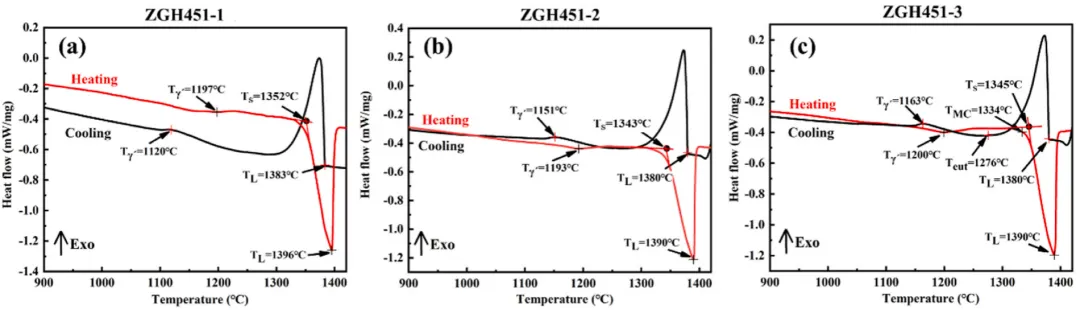
圖8. 從差示掃描量熱儀(DSC)測(cè)得的三種合金的升溫和降溫曲線。每條曲線上標(biāo)有顯著的相變溫度,并具體數(shù)值顯示在表4中。
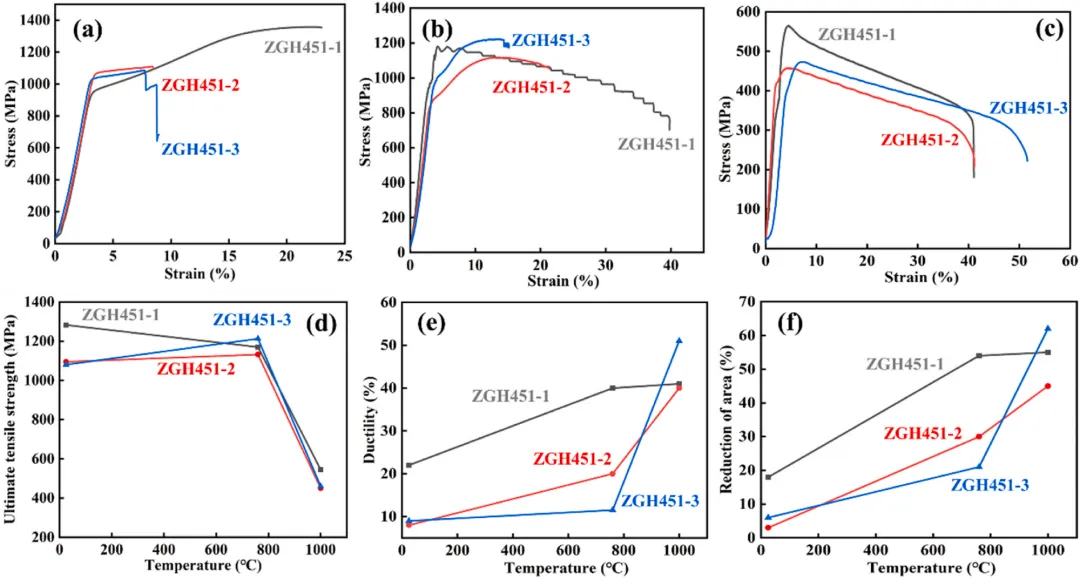
圖9. 三種合金在室溫和760至1000°C之間的成型拉伸性能。(a-c)顯示了經(jīng)過(guò)室溫、760°C和1000°C測(cè)試后的拉伸曲線。(d-e)展示了三種合金的抗拉強(qiáng)度、延性和斷面收縮率值的比較。
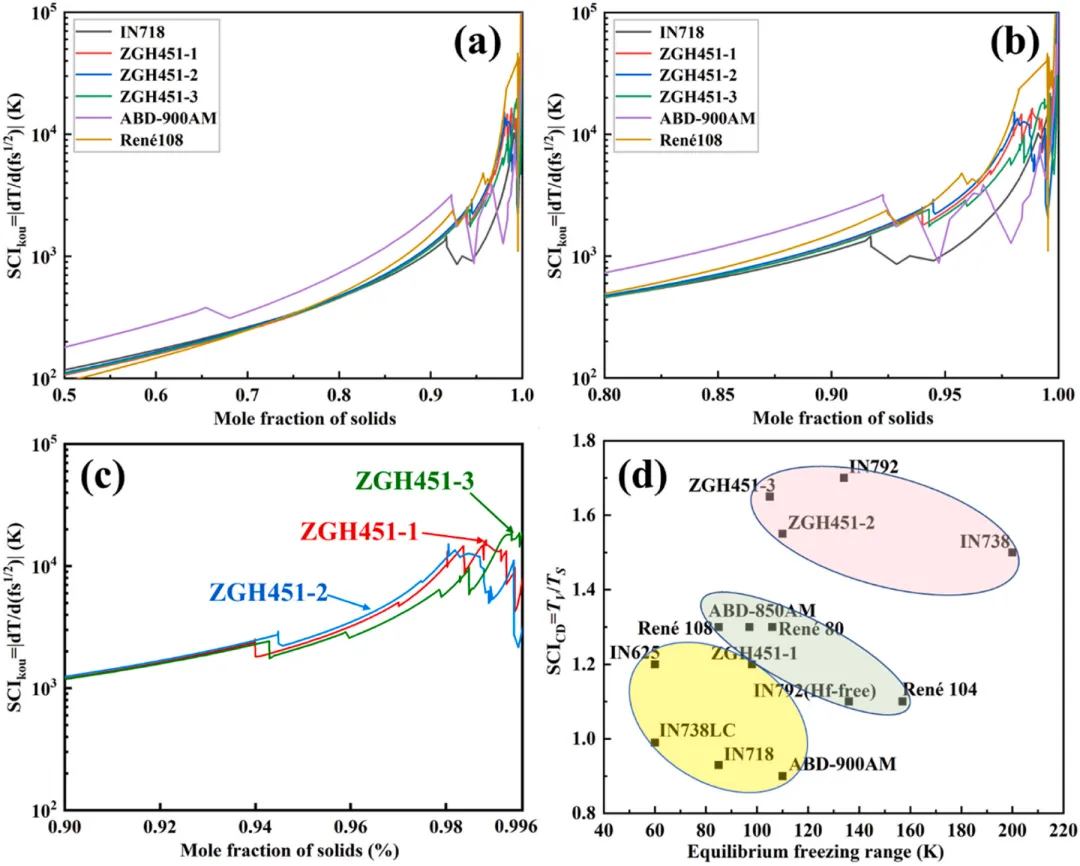
圖10. 基于平衡凍結(jié)范圍的凝固裂紋敏感性指數(shù)(Clyne & Davies (SCICD))和Kou (SCIKou)的計(jì)算結(jié)果,由Thermo-Calc和TCNI10數(shù)據(jù)庫(kù)計(jì)算得出。(a) 展示了在0.5–1.0的固相比下的SCIKou曲線概覽,(b) 是在0.8–1.0的固相比下的放大曲線。(c) 說(shuō)明了在固相比0.8–0.996的最后階段凝固中的SCIKou值。(d) 顯示了各種合金的SCICD和平衡凍結(jié)范圍值的分布。
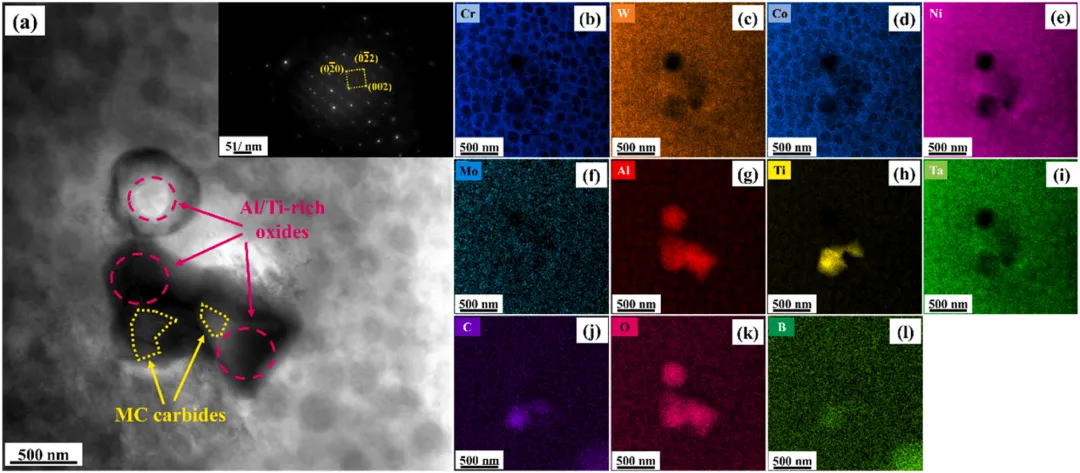
圖11. 通過(guò)透射電子顯微鏡獲得的合金ZGH451-1中碳化物的形貌、衍射圖樣和元素分布。(a) 展示了碳化物和氧化物的形貌。(b-l) 展示了所有元素的分布。
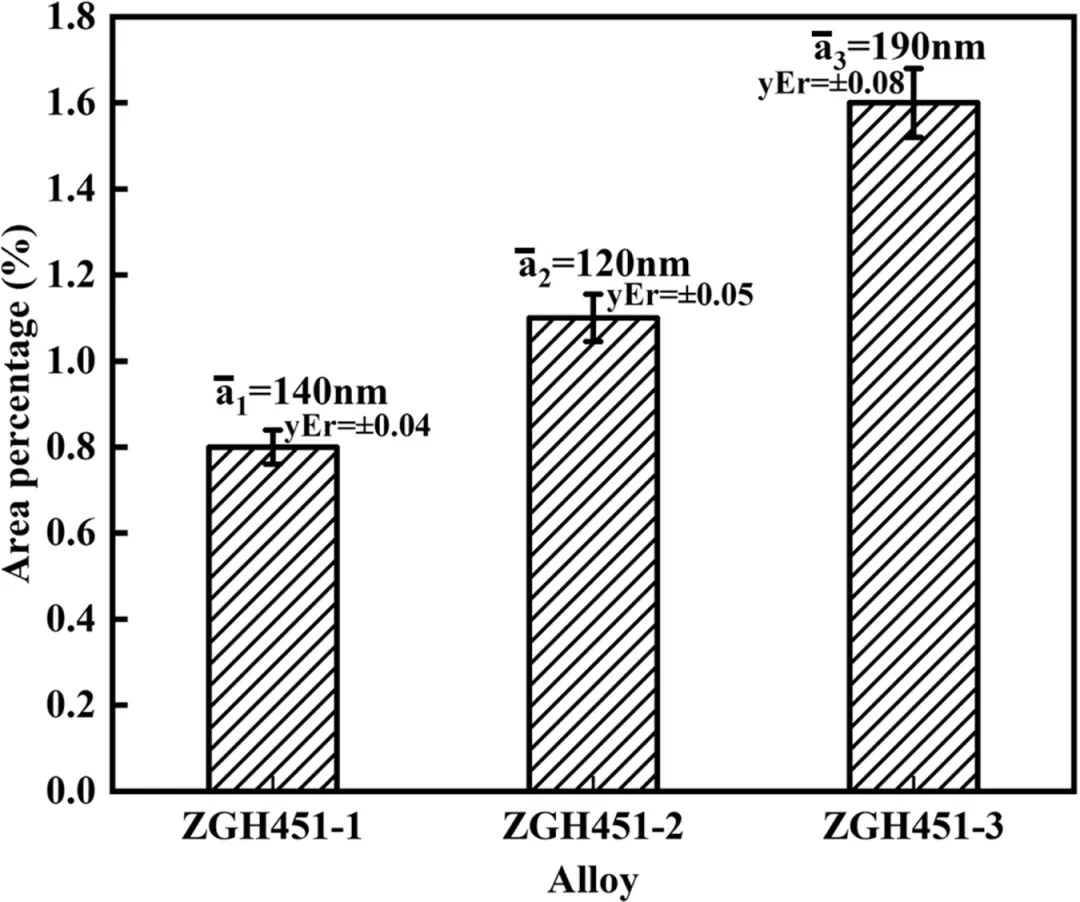
圖12. 三種合金中碳化物的尺寸和面積百分比(相當(dāng)于體積分?jǐn)?shù))。
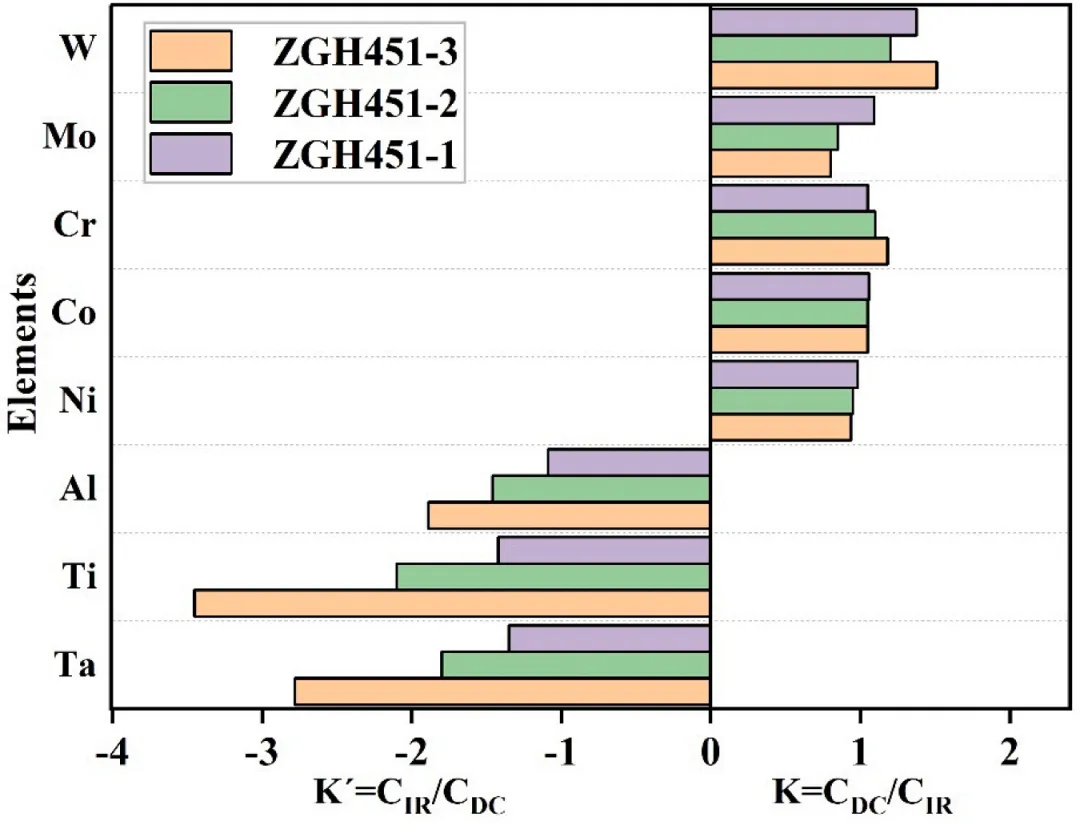
圖13. 通過(guò)K'和K的分配比反映出每種合金元素的偏聚行為。
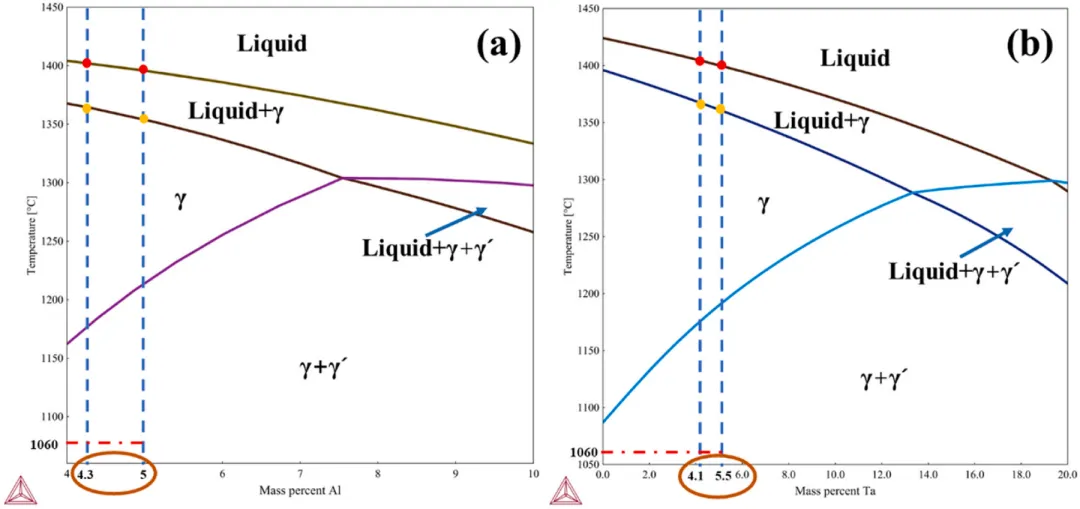
圖14. 利用Al(a)和Ta(b)的變量建立偽二元相圖。
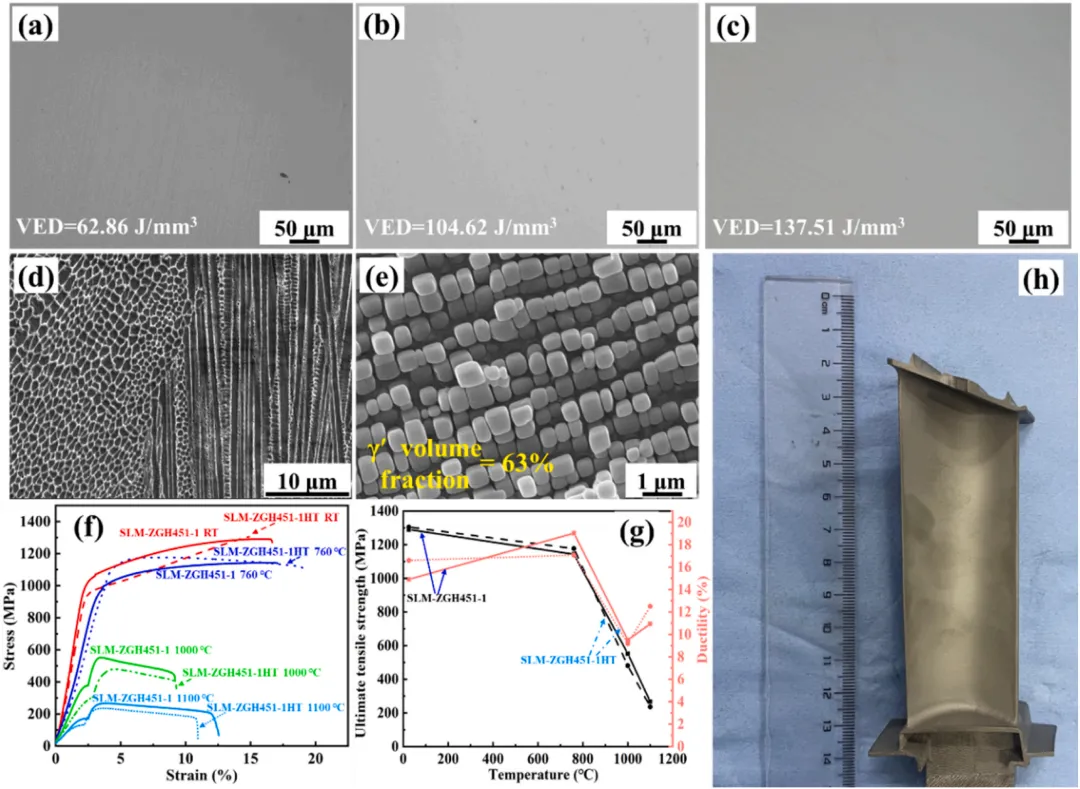
圖15. 對(duì)由SLM制造的ZGH451-1合金的構(gòu)建和熱處理微觀結(jié)構(gòu)的整體檢查和分析,觀察到的結(jié)構(gòu)垂直于構(gòu)建方向(X-Y平面)。(a-c)展示了在不同體積能量密度(VED)下X-Y平面的無(wú)裂紋結(jié)構(gòu)的金相顯微鏡圖像,(d, e)分別為構(gòu)建狀態(tài)和熱處理后的微觀結(jié)構(gòu)的掃描電鏡圖像。(f)顯示了從室溫到1100°C的構(gòu)建狀態(tài)和熱處理后的SLM ZGH451-1的拉伸曲線,(g)是相應(yīng)的抗拉強(qiáng)度和延性數(shù)值。(h) 由ZGH451-1合金通過(guò)SLM制造的具有復(fù)雜結(jié)構(gòu)的無(wú)裂紋渦輪葉片。
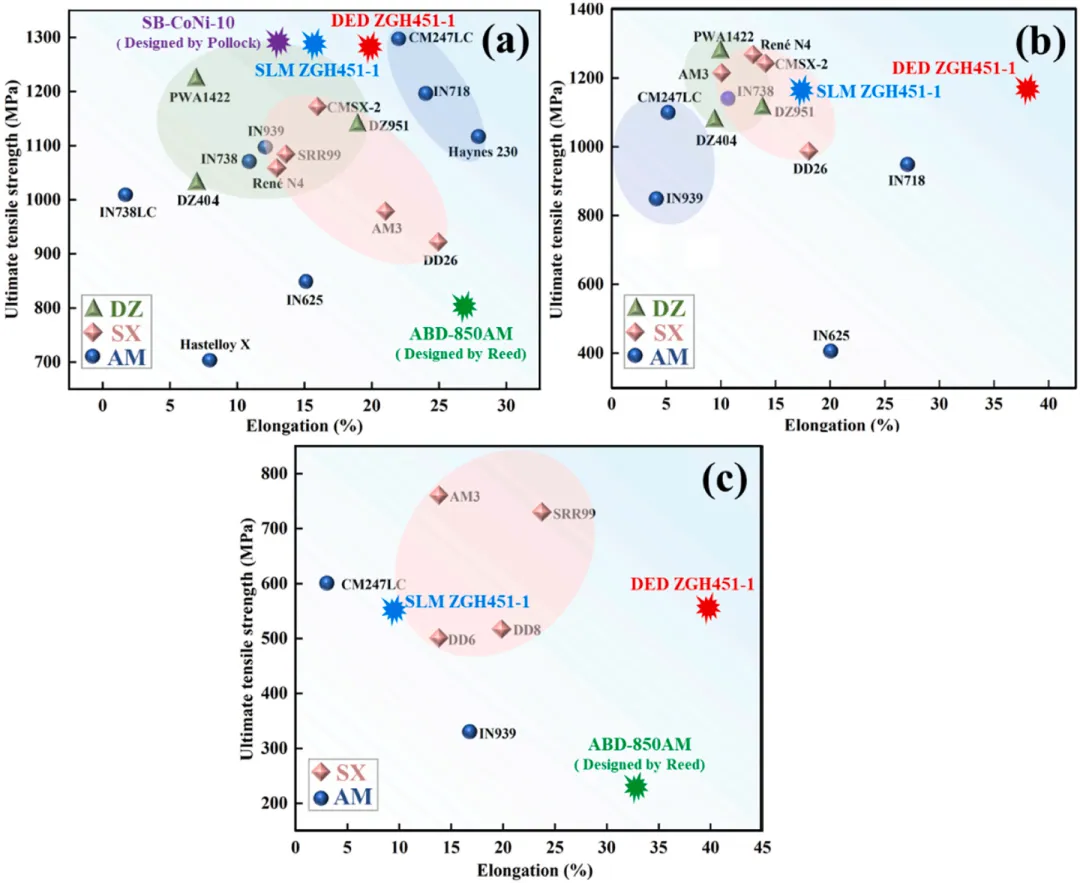
圖16. 將構(gòu)建狀態(tài)的ZGH451-1合金與報(bào)道的定向凝固(DZ,熱處理) [89–91],單晶(SX,熱處理)和增材制造高溫合金進(jìn)行室溫(a)、760°C(b)和1000°C(c)后的拉伸性能進(jìn)行比較。
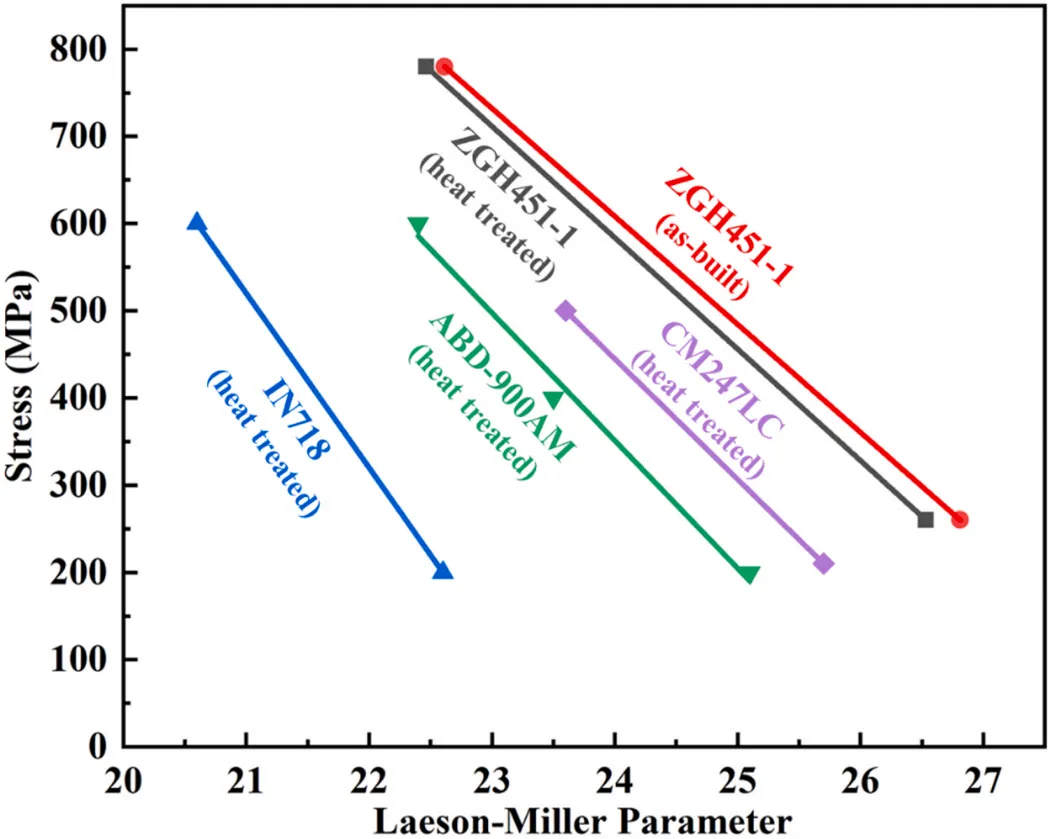
圖17. 基于Larson-Miller參數(shù)比較了報(bào)告的熱處理合金IN718、ABD-900AM、CM247LC 和構(gòu)建狀態(tài)的合金ZGH451-1的蠕變性能。