導(dǎo)讀:本文采用一種新穎靈活的方法制備了Mg/Al復(fù)合材料板。采用冷噴涂的方法在AZ31B鎂合金板上直接沉積7075鋁合金粉末,從而得到結(jié)合良好的Mg/Al復(fù)合板材。然后對噴射態(tài)復(fù)合材料板進(jìn)行熱軋(HR)以進(jìn)一步提高(軋制態(tài))力學(xué)性能。從滾動方向(RD)和橫向(TD)兩方面系統(tǒng)研究了噴射態(tài)和軋制態(tài)Mg/Al復(fù)合板材的界面組織、織構(gòu)演變、金屬間化合物(IMCs)形成、力學(xué)性能和斷裂行為。結(jié)果表明:CS + HR法制備的Mg/Al復(fù)合材料板的力學(xué)性能與傳統(tǒng)滾接、爆炸焊和擴(kuò)散焊等法制備的Mg/Al復(fù)合材料板相當(dāng),甚至優(yōu)于后者。噴射復(fù)合材料板材在界面處表現(xiàn)出較強(qiáng)的剪切結(jié)合強(qiáng)度,這是由CS過程引起的。HR增強(qiáng)了Al-Al顆粒間的結(jié)合,導(dǎo)致AZ31B Mg層晶粒細(xì)化。此外,在HR樣品界面形成條狀分布的內(nèi)膜細(xì)胞。結(jié)果表明,Al、Mg組份板以及復(fù)合材料板的極限抗拉強(qiáng)度(UTS)均有所提高,而剪切強(qiáng)度略有降低。并詳細(xì)研究了復(fù)合材料板的裂紋萌生和擴(kuò)展過程,以了解其斷裂機(jī)理。
近幾十年來,鎂及其合金因其自身的優(yōu)良性能而引起了人們的廣泛關(guān)注密度低,比強(qiáng)度高,電磁屏蔽性能好。鎂合金作為最輕的結(jié)構(gòu)金屬,在汽車、航空航天和電子工業(yè)中具有廣泛的應(yīng)用前景。然而,鎂合金的主要缺點(diǎn)之一是耐腐蝕性能差,這極大地限制了鎂合金的廣泛應(yīng)用。要解決這個問題,一個有效的解決辦法就是制造Mg/Al復(fù)合板材,其中鋁可以提供優(yōu)良的耐腐蝕性能,通過在其表面自然形成致密的保護(hù)性Al2O3膜。
目前,制備Mg/Al復(fù)合材料板的方法有輥焊、爆炸焊、擴(kuò)散焊、共擠、帶鑄等。顯然,爆炸焊接和擴(kuò)散連接可以形成良好的結(jié)合界面,具有較高的結(jié)合強(qiáng)度和較薄的IMCs。然而, 從生產(chǎn)效率、生產(chǎn)成本和環(huán)境保護(hù)等方面來看,這些工藝并不適合鎂鋁復(fù)合板材的工業(yè)化生產(chǎn)。輥式粘接是一種高效、經(jīng)濟(jì)、環(huán)保的粘接技術(shù)制造復(fù)合材料,適合大規(guī)模工業(yè)生產(chǎn)。但文獻(xiàn)表明,在HR過程中,Mg/Al界面處不可避免地會形成脆性的IMCs(如Al3Mg2, Mg17Al12),使其力學(xué)性能下降。例如Nie et al.在400℃熱軋后在200-400℃退火1-4 h制備了Al /Mg/ Al層壓板,結(jié)果表明界面處形成的厚IMCs大大降低了粘結(jié)強(qiáng)度和塑性。此外,在輥粘接前,必須對配合面進(jìn)行研磨,以去除表面氧化層。此外,原料板需要用鉚釘或焊接固定在一起,以防止軋制過程中的相對運(yùn)動。由于原料板之間缺乏預(yù)粘結(jié),通常需要真空爐進(jìn)行加熱,以防止界面氧化。因此,上述問題限制了軋制結(jié)合技術(shù)在制備高質(zhì)量Mg/Al復(fù)合材料板中的應(yīng)用。
CS作為一種很有前途的用于多種材料的固態(tài)沉積技術(shù),近年來受到了廣泛的關(guān)注。在CS過程中,原料粉末在高壓高溫推進(jìn)氣體的加速作用下,受到基體或預(yù)沉積層的沖擊。冷噴涂沉積的持續(xù)生長很大程度上依賴于顆粒-顆粒界面的嚴(yán)重塑性變形和絕熱剪切不穩(wěn)定性。在整個CS過程中,原料粉末的溫度保持在其熔點(diǎn)以下,從而避免了氧化、相變和最終鍍層的熱應(yīng)力。迄今為止,已成功制備出各種組織致密、力學(xué)性能優(yōu)良的金屬鍍層。其中包括純銅、鋁、鎳、鋅等及其合金。
在前人工作的基礎(chǔ)上,CS與HR相結(jié)合(CS+HR)已被證明是一種制備金屬層合板的有效方法。Zhao et al.利用CS在鋼板上沉積純鈦粉末成功制備鈦/鋼復(fù)合板,并研究了熱軋和噴淋后退火處理對其組織和力學(xué)性能的影響。采用CS+HR法制備層合材料,可以很好地控制各組成金屬層的厚度。此外,高速顆粒撞擊(沉積過程中)可以打破基材和原料粉末表面的氧化膜。該冷噴層壓復(fù)合材料不僅可以作為某一用途的成品,還可以作為軋輥粘接的中間產(chǎn)品。也就是說,可以用CS代替?zhèn)鹘y(tǒng)軋制工藝中的鉚釘固定和焊接工序,實(shí)現(xiàn)各組成金屬板之間的緊密無空洞結(jié)合。因此,在軋制過程中不再需要真空爐,避免了不必要的界面氧化。
據(jù)作者所知,目前還沒有通過CS+HR制備Mg/Al復(fù)合板材的嘗試。在此,中科院金屬所Jiqiang Wang教授團(tuán)隊(duì)探索CS+HR制備商業(yè)應(yīng)用的Mg/Al復(fù)合板材的可行性。研究了不同工藝條件下Mg/Al復(fù)合材料的RD和TD界面組織和力學(xué)性能。利用混合物規(guī)則(ROM)預(yù)測Mg/Al復(fù)合材料板的抗靜電強(qiáng)度,并將預(yù)測值與實(shí)驗(yàn)值進(jìn)行比較。并詳細(xì)研究了復(fù)合材料板的裂紋萌生和擴(kuò)展過程,以了解其斷裂機(jī)理。相關(guān)研究成果以題“An innovative and flexible approach to fabricate Mg/Al composite plates: Cold spraying and hot rolling post-treatment”發(fā)表在金屬頂刊Materials Science and Engineering: A上。
鏈接:https://doi.org/10.1016/j.msea.2022.143515
1.采用冷噴涂技術(shù)成功地制備了界面結(jié)合良好的(預(yù)粘合)Mg/Al復(fù)合材料板。7075 Al鍍層與AZ31B Mg鍍層之間形成了較強(qiáng)的機(jī)械聯(lián)鎖,這是由CS過程中的嚴(yán)重沖擊引起的。噴射態(tài)Mg/Al復(fù)合板材的抗拉強(qiáng)度、EL強(qiáng)度和剪切強(qiáng)度分別為262 + 5.7 MPa、4.4 + 0.2%和127 + 6.5 MPa。
2.熱軋后,板條分布的IMCs、新的結(jié)合界面和微孔交替分布在原始界面上。IMCs由AlsMg2和Mg17Al12組成。
3.熱軋強(qiáng)化了Al-Al顆粒間的結(jié)合,導(dǎo)致AZ31B Mg層晶粒細(xì)化。結(jié)果表明,Al、Mg組份板及復(fù)合材料板(RD: 369 + 7.6 MPa, TD: 366 + 14 MPa)的抗壓強(qiáng)度均有所提高。對于噴涂和軋制后的RD樣品,Pre. UTS(由ROM預(yù)測)和Exp. UTS很好地一致。然而,As - Roll TD樣本的Pre. UTS略低于Exp. UTS,因?yàn)镽OM沒有考慮到條帶分布的IMC的影響。
4.斷裂后,Mg/Al復(fù)合板材沒有發(fā)生完全的分層,EL值始終保持在7075 Al和AZ31B Mg組份之間。由于7075層固有的低延性,裂紋最初產(chǎn)生于7075層的外表面,并向界面擴(kuò)展。
圖1 冷噴涂(a)和熱軋(b)工藝的示意圖。面板(c)顯示了軋制時Mg/Al復(fù)合材料板的數(shù)字圖像不同的觀點(diǎn)。
圖2 拉伸試樣的原理圖和精確尺寸(a)剪切(b)試驗(yàn)。
圖3 7075原料的SEM顯微圖(a-c)和粒度分布(d)粉。圖(e)為S1和S2的EDS點(diǎn)分析結(jié)果。
圖4 ND-RD (c, d)和ND-TD (e, f)面噴射(a)和軋制(a) Mg/Al復(fù)合材料板的截面SEM圖。圖(b)顯示了圖(a)的EDS映射結(jié)果。圖(g-i)顯示了分別對新鍵合界面、IMCs和孔隙進(jìn)行的EDS線掃描。面板(j)匯總了面板(d)和(f)的點(diǎn)分析結(jié)果。
圖5 噴射態(tài)和軋制態(tài)Mg/Al復(fù)合材料板的XRD譜圖界面區(qū)域。
圖6 研究了噴射態(tài)(a, b)和軋制態(tài)(c, d) Mg/Al復(fù)合材料板沿界面分離的斷口形貌。界面IMCs分布示意圖(e)。
圖7 圖像質(zhì)量圖像(a, d),反極圖(b, e)和極圖(c, f)噴射態(tài)7075 Al鍍層和接收態(tài)AZ31B Mg鍍層圖。
圖8 圖像質(zhì)量圖像和反向極點(diǎn)圖取自于噴射時(a, d),軋制時RD (b, e)和軋制時RD (c, f)復(fù)合材料板的截面積。面板(g-i)顯示了Mg層的極線圖。
圖9 不同工藝條件下Mg/Al復(fù)合材料板界面附近的維氏顯微硬度分布:噴態(tài)(黑色)、軋制態(tài)(紅色)和軋制態(tài)(藍(lán)色)。圖中為典型的7075 Al、AZ31B Mg和界面壓痕的SEM圖像。
圖10 噴射態(tài)(a)、軋制態(tài)(b)、軋制態(tài)(c)復(fù)合材料板和薄板的典型工程應(yīng)力-應(yīng)變曲線。抗剪強(qiáng)度(d)與剪切粘結(jié)強(qiáng)度(e)的柱狀圖。
圖11 拉伸試樣的斷裂形貌: 噴射態(tài)(a-d); 軋制態(tài)RD (e-h); 軋制態(tài)TD (i-l).
圖12 不同應(yīng)變水平下拉伸試樣的OM截面圖像,它代表了復(fù)合材料板的斷裂過程:裂紋萌生(a)、裂紋擴(kuò)展(b)和斷裂(c)。
圖13 剪切試樣的斷裂形貌:噴射態(tài)(a, d)、軋制態(tài)RD (b, e)和軋制態(tài)TD (c, f)。不同加工條件下的界面斷裂示意圖:噴射態(tài)(g)、軋制態(tài)RD (h)和軋制態(tài)TD
綜上所述,首次采用冷噴涂與熱軋相結(jié)合的工藝制備出了具有優(yōu)良組織和力學(xué)性能的Mg/Al復(fù)合板材。研究了Mg/Al復(fù)合材料在不同工藝階段的組織和力學(xué)性能。噴涂后的樣品具有較高的剪切強(qiáng)度(127 + 6.5 MPa),這是由于其具有較強(qiáng)的機(jī)械聯(lián)鎖作用。熱軋后,RD (78 + 6.9 MPa)和TD (124 + 4.6 MPa)的剪切粘結(jié)強(qiáng)度均有所下降。軋制態(tài)RD和軋制態(tài)TD試樣剪切粘結(jié)強(qiáng)度的差異可能與內(nèi)模組織的帶材分布形態(tài)有關(guān)。
免責(zé)聲明:本網(wǎng)站所轉(zhuǎn)載的文字、圖片與視頻資料版權(quán)歸原創(chuàng)作者所有,如果涉及侵權(quán),請第一時間聯(lián)系本網(wǎng)刪除。
相關(guān)文章
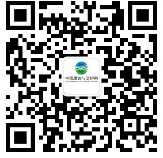
官方微信
《腐蝕與防護(hù)網(wǎng)電子期刊》征訂啟事
- 投稿聯(lián)系:編輯部
- 電話:010-62316606-806
- 郵箱:fsfhzy666@163.com
- 腐蝕與防護(hù)網(wǎng)官方QQ群:140808414
文章推薦
點(diǎn)擊排行
PPT新聞
“海洋金屬”——鈦合金在艦船的
點(diǎn)擊數(shù):8148
腐蝕與“海上絲綢之路”
點(diǎn)擊數(shù):6486