在過去的一百多年以來,金屬的疲勞失效問題一直是工業界關注的核心問題之一。統計表明,工業構件的失效中有80-90%屬于疲勞失效。發生疲勞失效的構件一般承受動態載荷,如高鐵的車軸、發動機葉片等,其工作應力往往顯著低于材料的屈服應力,構件失效一般發生在104-107,甚至109周次以上的循環載荷。金屬的疲勞過程一般為:構件內部微缺陷或局部應力集中→局部塑性變形→局部微裂紋形成和發展→宏觀裂紋出現→構件失效。現有的無損檢測方法只能檢測到長度2mm以上的宏觀裂紋,對于尺寸更小的微裂紋,目前還缺少有效的檢測方法。
最近,北京大學工學院李法新課題組在金屬疲勞領域取得了突破性進展,他們提出采用測量內耗的方法來監測鋁合金的疲勞失效,相關論文“ Detecting fatigue in aluminum alloys based on internal friction measurement using an electromechanical impedance method”作為主編精選(Editor's Pick)發表于Journal of Applied Physics。課題組2019級碩士生唐驥驊和2018級博士生謝明宇為論文的共同第一作者。
李法新課題組前期提出了基于壓電機電阻抗、既準又快的模量內耗測量新方法(Rev Sci Instrum 2020, Editor's Pick, https://doi.org/10.1063/1.5135360),該方法測量模量的精度比ASTM標準高一個量級,測量內耗的誤差小于2E-5。在此基礎上,他們提出采用測量內耗的手段來監測金屬的疲勞過程。實驗結果表明,鋁合金在拉壓對稱的疲勞加載過程中,內耗隨加載的周次單調增加,破壞前的內耗值可以達到初始值的3倍以上(圖1b),這表明內耗對于金屬的疲勞損傷非常敏感。相比之下,樣品的共振頻率在失效前僅降低了不到2%(圖1c)。不同的樣品在疲勞過程中內耗的變化曲線可能相差很大(圖2),但有一點是共同的,即在疲勞失效的后段,內耗隨疲勞周次增加得很快,這一階段可認為是微裂紋的形成和發展過程。
圖1. 典型鋁合金構件在不同疲勞周次加載后的:(a)電納曲線;(b)內耗;(c)共振頻率。
圖2. 另外2個鋁合金樣品在疲勞過程中的內耗和共振頻率變化
基于鋁合金疲勞監測的實驗結果,李法新課題組提出了基于內耗測量的金屬疲勞失效預警準則,可在構件50-80%疲勞壽命時給出有效的預警。而且,由于微裂紋導致的疲勞失效是大多數結構材料失效的主要形式,該疲勞失效預警準則同樣可適用于復合材料、陶瓷等其它結構材料。進一步,由于大部分機械類損傷失效可以歸為材料內部連接的松動(疲勞),或者不同構件之間的連接松動(焊點失效,螺栓松動,膠層劣化等等),而這些內部或外部連接的松動將顯著增大材料的內耗(或結構的阻尼)。因此,測量構件的內耗(或阻尼)可有效地判斷構件的機械損傷,這比傳統的測量頻率(或模量)的方法更為敏感和有效。
免責聲明:本網站所轉載的文字、圖片與視頻資料版權歸原創作者所有,如果涉及侵權,請第一時間聯系本網刪除。
相關文章
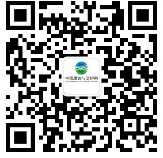
官方微信
《中國腐蝕與防護網電子期刊》征訂啟事
- 投稿聯系:編輯部
- 電話:010-62316606-806
- 郵箱:fsfhzy666@163.com
- 中國腐蝕與防護網官方QQ群:140808414
點擊排行
PPT新聞
“海洋金屬”——鈦合金在艦船的
點擊數:7437
腐蝕與“海上絲綢之路”
點擊數:5962